UZYSKAJ PERFEKCYJNE WYKOŃCZENIE WYROBÓW PRODUKOWANYCH PRZYROSTOWO W POLERKACH WIROWYCH!
Zgodnie z normą DIN 8580 druk 3D jest jednym z podstawowych procesów produkcyjnych, w których bryła o geometrycznie określonym kształcie jest wytwarzana z bezkształtnego materiału. W procesie wykorzystuje się szeroką gamę materiałów, takich jak metale, tworzywa sztuczne i ceramika. Odkryte ponad 30 lat temu addytywne procesy produkcyjne są obecnie na tyle rozwinięte , że stopniowo zyskują na znaczeniu w produkcji przemysłowej. Niezależnie od tego, czy chodzi o prototypy, czy produkcję seryjną, wytwarzanie przyrostowe jest stosowane we wszystkich branżach w celu uzyskania widocznych i funkcjonalnych komponentów, a także niestandardowych produktów projektowych. Części jubilerskie, implanty dentystyczne, wkładki do uszu i łopatki silnika to tylko kilka przykładów.
Im większe możliwości tego procesu wytwarzania, tym wyższe stają się parametry obrabianego przedmiotu. Jakość seryjna jest najbardziej istotna, co oznacza, że jakość powierzchni, powtarzalność i niezawodność procesu są w centrum uwagi po obróbce.
We wszystkich procesach drukowania 3D warstwy komponentu są nakładane selektywnie, jedna po drugiej. Ta zasada sprawia, że formowanie komponentów jest zarówno elastyczne, jak i dostosowane do indywidualnych potrzeb. Części drukowane w 3D jako warstwowe mają strukturę powierzchni charakteryzującą się prążkami, porami, szczelinami i ubytkami.
Trzy klasyczne rozwiązania poprawiające jakość powierzchni i zmniejszające efekt schodów
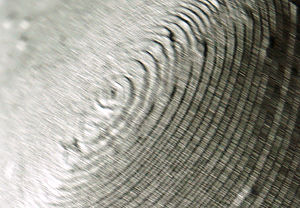
Konwencjonalne rozwiązania to wykończenie ręczne, odparowywanie powierzchni rozpuszczalnikiem lub obróbka masowa, na przykład szlifowanie wibracyjne.
Wadą pierwszej opcji jest to, że czynnik ludzki podczas ręcznego wygładzania i polerowania nie jest opłacalny pod względem powtarzalności i czasów procesu.
Chemiczne procesy wygładzania wymagają czasochłonnego, a zatem kosztownego przygotowania, wymiany i utylizacji rozpuszczalników. Koszty użytkowe są również wyższe niż w przypadku innych technik obróbki wykończeniowej, co znacznie zmniejsza sens wydajnej produkcji masowej.
Z drugiej strony wykańczanie wibracyjne nie wymaga użycia środków chemicznych. Jednak czasy obróbki mogą być bardzo długie i przez to często nieekonomiczne.
Czy jest więc alternatywa? Czy można uzyskać jakość seryjną na częściach wydrukowanych w 3D wykonanych z różnych materiałów? Z pewnością można!
Drei klassische Lösungsansätze zur Verbesserung der Oberflächenqualität und zur Reduzierung des Treppenstufeneffekts
Als klassische Lösungsansätze gelten die händische Nachbearbeitung, das Bedampfen mit Lösungsmittel oder Gleitschleifen, etwa im Vibrator.
Nachteil des erstgenannten manuellen Glättens und Polierens ist, dass durch den Faktor Mensch die Wiederholgenauigkeit und Prozesszeiten keine wirtschaftliche Fertigung ermöglichen.
Beim chemischen Glättungsverfahren müssen die Lösungsmittel in den Anlagen arbeitsaufwändig und somit kostenintensiv aufbereitet, getauscht und entsorgt werden. Außerdem sind die Anschaffungskosten höher als bei anderen Nachbearbeitungsverfahren, was gesamtheitlich betrachtet dem Ziel der effizienten Serienfertigung im Weg steht.
Beim Gleitschleifen im Vibrator werden hingegen keine Chemikalien eingesetzt, aber es kommt zu sehr langen und dadurch oftmals unwirtschaftlichen Prozesszeiten. Gibt es eine alternative Lösung, um additiv gefertigte Teile aus unterschiedlichen Materialien in Serienqualität zu erhalten? Ja, die gibt es!
Polerki wirowe OTEC bardzo szybko uzyskują jednorodne powierzchnie bez użycia środków chemicznych.
Polerki wirowe OTEC znacznie szybciej ujednolicają gąbczaste, porowate powierzchnie, wygładzając je i polerując.
Sprowadza się to do mechanicznej zasady działania naszych maszyn: detale do wielkości pięści (w zależności od konfiguracji maszyny) są umieszczane w niebieskim pojemniku roboczym w ilości masowej lub pojedynczo wraz z wsadem szlifierskim lub polerskim odpowiednim do geometrii obrabianego przedmiotu.
Na spodzie pojemnika znajduje się dysk na łożysku. Podczas obrotu dysku na dnie nieruchomego pojemnika, jego zawartość wprawiana jest w ruch w postaci toroidalnego przepływu. Wirowanie wyrobów i ścierniwa sprawia, że jest to bardzo intensywny i czysto mechaniczny proces.
Często kopiowana, nigdy z sukcesem: seria OTEC CF jest znana z elastyczności aplikacji, powtarzalności i niezawodności procesu.
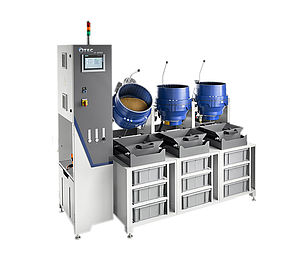
Elastyczny przebieg pracy: elementy obrabiane i ścierniwo można łatwo wymienić w każdym pojemniku. Maszyna jest modułowa, dzięki czemu można równolegle wykonywać różne etapy obróbki końcowej w różnych pojemnikach, niezależnie od tego, czy obrabiane elementy są takie same.
Stałe parametry gwarantowane za każdym razem: centralna jednostka sterująca maszyny umożliwia przechowywanie i monitorowanie parametrów procesu specyficznych dla przedmiotu obrabianego, które można uruchomić za naciśnięciem przycisku.
Czas to pieniądz!
W porównaniu z wykańczaniem wibracyjnym, polerki wirowe OTEC mają znacznie wyższy poziom ścierania mechanicznego. Dla producentów części drukowanych w 3D oznacza to krótsze czasy procesu - od 5 do 10 razy.
W przeciwieństwie do wygładzania chemicznego, nasze maszyny CF nie używają agresywnych środków chemicznych, takich jak rozpuszczalniki. Są bezpieczne w obsłudze, upraszczają przepływ pracy i oszczędzają czas. Co więcej, są tańsze w zakupie i obsłudze. Krótko mówiąc, obniżają koszty jednostkowe produkcji seryjnej.
Nasze maszyny ograniczają ręczną obróbkę do absolutnego minimum, jeśli nie do zera. Zależy to w dużej mierze od danego zastosowania i wymagań dotyczących wykończenia. Ogólnie rzecz biorąc, powtarzalna, niezawodna obróbka mechaniczna w polerkach wirowych obniża koszty pracy ręcznej o 80%. Jedynie końcowe polerowanie - na przykład w przypadku biżuterii - musi być wykonane ręcznie.
Przykład obróbki w CF: wyroby metalowe wytworzone metodą SLS
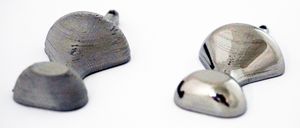
Podczas obróbki wyrobów metalowych wydrukowanych metodą SLS, polerka wirowa OTEC osiągnęła średni czas obróbki 1 -2 godziny na partię.
Przykład obróbki w CF: drukowane 3D plastikowe wkładki douszne
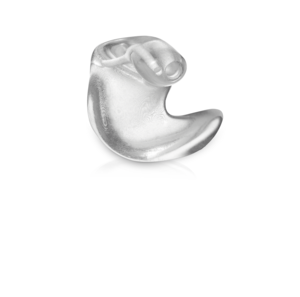
W zależności od ilości wyrobów i ich stanu początkowego można stosować różne materiały ścierne i czasy obróbki. Średni czas trwania każdego etapu procesu to 1–2 godziny. W zależności od maszyny można jednocześnie obrabiać większe partie. Od małych serii po produkcję masową, seria OTEC CF jest idealnym wyborem.
MOBILNA STACJA ODSIEWU UNISEPA – KOMPAKTOWA I ELASTYCZNA
Nowa wibracyjna stacja odsiewu UNISEPA od OTEC to uniwersalne rozwiązanie do oddzielania wsadu od szerokiej gamy wyrobów. Wyposażona w regulacje przepływu, częstotliwość i amplitudę wibracji UNISEPA poradzi sobie z każdym zadaniem odsiewu.
Film z pracy CF i Unisepa (Youtube)
Każdy wyrób jest inny, dlatego przetestuj nas
Wyślij do nas próbki i pozwól naszym ekspertom w laboratorium OTEC dostosować twój własny proces obróbki.