OTEC News
Press releases
Alongside company news you'll find solutions to some intriguing and tricky surface technology issues – simple concise, practical advice on deburring, grinding, smoothing and polishing.
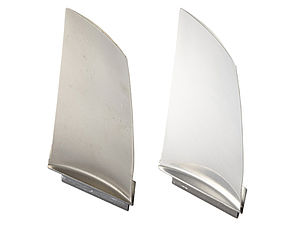
12/2018: Engine Blades
Turbine and Compressor blades - Safer and more efficient with an OTEC finish
Engine blades are subject to high temperatures and pressures. Manufacturers have therefore implemented strict regulations for the production and processing methods used. OTEC has developed a special process to improve the efficiency and safety of engine blades. The surface of the blade can be smoothed and the edges rounded precisely in a single operation. The surface treatment of engine blades takes only a few minutes and can prolong their service life.
more...
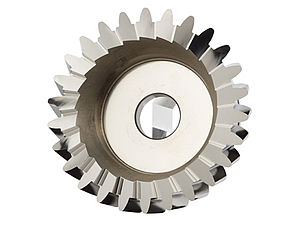
10/2018: Skiving cutters for gear wheel production
Surface finish for uniform cutting edges and polished cutting faces
Skiving cutters are used to produce gear wheels. Surface processing focuses on low chipping and a uniform rounding of the tooth heads and edges. Polishing and smoothing the cutting surfaces in the tooth profile allows chips to flow off better during gear wheel production. The smooth surface also significantly improves the coating adhesion of carbide layers to be applied. Polishing and rounding of gear wheels in the stream finishing machine usually takes only a few minutes.
more...
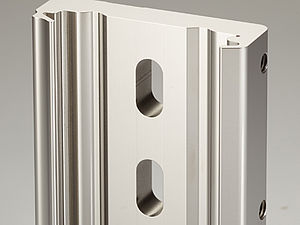
08/2018: PUNCHING DIES
SUPERIOR SURFACE QUALITY ENSURES HIGH OUTPUT
A punching die’s surface quality is essential for smooth and efficient stamping, which is why the surface processing methods for these tools are constantly being refined. OTEC offers machines and process technology for smoothing and polishing - for superior surface quality and a perfect contoured surface. The interaction between processing by OTEC and the coating can increase the tool’s output 10-fold.
more...
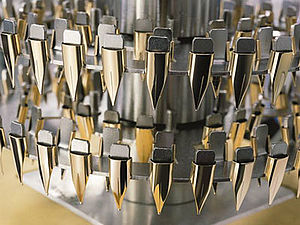
06/2018: OTEC FINISH FOR LAMY FOUNTAIN PEN NIBS
CUSTOMISED PROCESS FLOW FOR ELEGANT DESIGN AND OPTIMUM FUNCTIONALITY
OTEC was able to develop an individual process to grind and polish the surface areas of Lamy's nibs to achieve a perfect finish. The nibs are processed in OTEC CF disc finishing machines in a multi-stage procedure. It is only through this that they meet the high quality requirements of the Lamy brand. The advantages of the procedure lie mainly in the speed, reliability and process safety. Thanks to the customised process it is possible to remove ghost lines and polish the nibs to a gloss.
more...
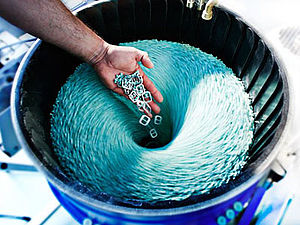
04/2018: FASHION JEWELLERY
A SPARKLING BRILLIANCE FOR ACCESSORIES
Fashion jewellery such as decorative clasps and decorations on handbags, as well as rivets and belt buckles demand maximum precision from the manufacturing process. They are often made from die cast zamak, brass or steel. OTEC offers a cost-effective process for the surface refinement of fashion jewellery and acces-sories: its disc finishing machines achieve the highest surface quality in the shortest possible time. The jewellery is polished to a high gloss, producing an impressively perfect finish.
more...
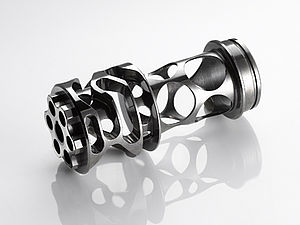
04/2018: IN POLE-POSITION BY MINIMIZING FRICITON
OTEC CONFINES FRICTION TO THE RACETRACK
While engineers in the automotive industry are always looking for ways to optimise efficiency, smooth running and emission management, the focus in motorsport is on pushing performance to its limits. As an international technology leader in mass finishing, OTEC designs and builds systems that reduce friction between components, benefiting both the premium car segment and motorsport. The heat, stresses and material abrasion caused by friction are detrimental to the precision and service life of all components. Lower friction means less wear, smoother power delivery and better energy consumption. The aim is always to minimise the influence of friction on the system as far as possible. Component properties of camshafts, gear wheels, valves, shift drum, worm shaft and gear parts can be improved by deburring, rounding, smoothing and polishing with OTEC finishing process.
more...
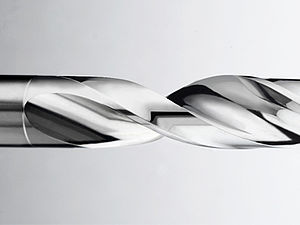
02/2018: POLISHING CARBIDE TOOLS
HIGH GLOSS IN THE FLUTE
OTEC machines allow the quality of carbide tools to be improved considerably. The special procedure enables the chip grooves of carbide cutters and drill bits, for example, to be polished to a high gloss. The polish enables higher cutting values and feed rates to be achieved. The OTEC process not only ensures a smooth, polished flute, but also improves the adhesion of coatings.
more...
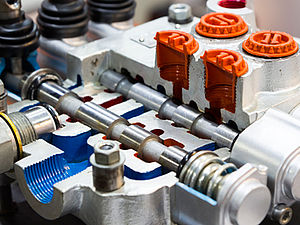
01/2018: VALVE SPOOLS
SMOOTHING FOR HIGH CONTACT RATIO
For the surface quality of the valve spool it is not only important to deburr and smooth, but also perform defined rounding of the edges. By smoothing the roughness peaks high contact ratios are achieved, leading to less friction and less wear. The result is a more reliable sealing surface at the edges which control the volume flows in the valve. The smooth surface also ensures less leakage when overflowing and lower leak oil values. Deburring, rounding and smoothing of the valve spools reduce friction on the valve.
more...