NIEZAWODNY I POWTARZALNY PROCES: ZAOKRĄGLANIE KRAWĘDZI GNIAZD W KSZTAŁCIE JODŁY
Whitepaper Aerospace
GNIAZDA DYSKU I ZAMKI ŁOPATEK– ODWZOROWANIE KSZTAŁTU JEST PRIORYTETEM NUMER 1
Dyski turbin i kompresorów posiadają gniazda w kształcie jodełki, w które montowane są łopatki turbiny. Standardowe metody produkcji tych gniazd montażowych to przeciąganie, cięcie drutem lub frezowanie. Ale te techniki powodują powstawanie zadziorów i ostrych krawędzi w gnieździe. Aby zapewnić bezbłędny montaż i zapobiec skaleczeniom, krawędzie gniazda i zamka łopatki muszą być pozbawione zadziorów i zaokrąglone określonym promieniem. Tylko w ten sposób można zagwarantować prawidłowe działanie komponentów. W szczególności powierzchnie nacisku, z którymi stykają się zamki łopatek w gniazdach dysku podczas pracy, podlegają bardzo wąskim tolerancjom 10–20 µm. Aby łopatki były idealnie ustawione, konieczne jest zapobieganie zmianom kształtu powierzchni nacisku podczas gratowania i zaokrąglania.
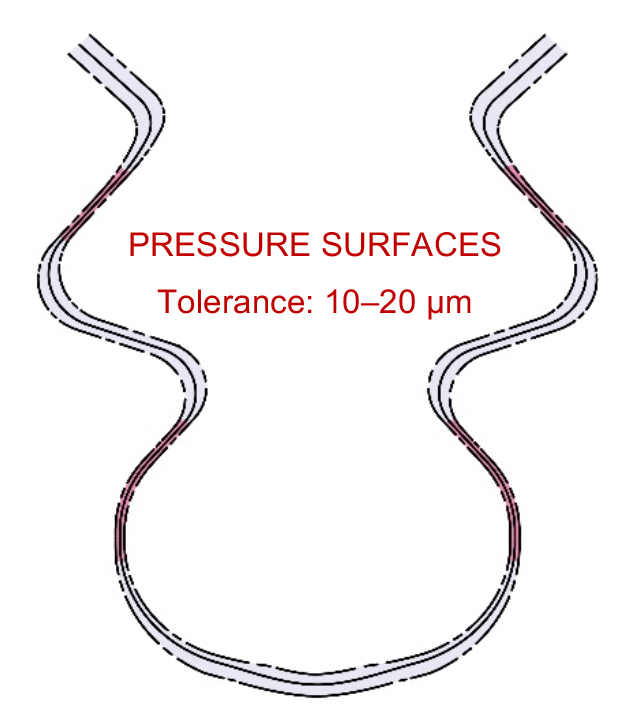
POWTARZALNOŚĆ – DLACZEGO ZROBOTYZOWANY PROCES NIE JEST NAJLEPSZYM WYBOREM
Standardową obróbkąwykończeniową dla tego etapu procesu jest mechaniczne, półzrobotyzowane gratowanie i zaokrąglanie za pomocą ściernic lub szczotek. Narzędzia te zużywały się z upływem czasu, powodując niespójne wyniki obróbki przez cały okres ich eksploatacji. Na przykład ostre krawędzie mogą odcinać końcówki szczotek, utrudniać przewidywanie ich zużycia, a tym samym prowadzić do różnych wyników, a także do silnego zanieczyszczenia procesu z powodu pozostałości szczotek. Podobnie ściernice podlegają nierównomiernemu usuwaniu materiału, co musi kompensować ruchy robota, a ścieranie powoduje zanieczyszczenie procesu.
W przypadku skomplikowanych geometrii przedmiotu obrabianego wyniki zaokrąglania są często asymetryczne, ponieważ ściernice lub szczotki nie mogą być dokładnie dopasowane do dokładnej geometrii rowka pod choinkę lub ponieważ w ogóle nie mogą dostać się do trudno dostępnych miejsc. Te asymetryczne i niespójne wyniki zaokrąglania często nie spełniają tolerancji, powodują zmiany kształtu, a tym samym zwiększają zarówno ilość części odpadowych, jak i koszty.
PORÓWNANIE ALTERNATYWNYCH PROCESÓW OBRÓBKI
W poszukiwaniu alternatywnego procesu obróbki z zadawalającymi wynikami, producent silników współpracował z OTEC, aby ocenić dwie różne technologie obróbki masowej.
Pierwszy proces, w wibratorze kołowym, okazał się nieprzydatny do aplikacji: nawet po kilku godzinach obróbki nie był w stanie zapewnić załamania wszystkich krawędzi w zakresie tolerancji. Uzyskane w testach zaokrąglenia nie były ani symetryczne, ani powtarzalne. Co więcej, zwiększony poziom hałasu i związane z nim wibracje stanowiły problem, biorąc pod uwagę, że w pobliżu używane były czułe urządzenia pomiarowe.
Drugi proces, w polerce strumieniowej OTEC, szybko osiągnął bardzo obiecujące wyniki w pierwszej próbie. Dzięki precyzyjnemu pozycjonowaniu elementu wszystkie załamania krawędzi były w granicach tolerancji w ciągu zaledwie 15 minut, z wysoce symetrycznym zaokrągleniem wzdłuż całej krawędzi. Dodatkowe testy potwierdziły, że proces był powtarzalny i stabilny. Zmienność kształtu była mniejsza niż 1 µm – tak mała, że nie była wymagana ani jedna korekta w parametrach procesu. Również, niski poziomie hałasu i wibracji podczas obróbki umożliwiał pracę w pobliżu czułych urządzeń pomiarowych.
Poniższe zalety zostały potwierdzone już przez kilku producentów silników :
- Krótki process obróbki to tylko 15 minut
- Bardzo symetryczne, jednolite zaokrąglenia
- Stabilne, powtarzalne parametry procesu
- Usuwanie zadziorów bez zanieczyszczeń
- Minimalna zmienność kształtu w powierzchniach nacisku gniazd jodłowych
- Niezawodna, mierzalna zgodność z wąskimi tolerancjami poniżej 1 µm
- Czysto mechaniczne usuwanie materiału, bez użycia chemicznych przyspieszaczy procesów
JAK DZIAŁA OBRÓBKA STRUMIENIOWA?
W mechanicznej obróbce strumieniowej, która została opracowana przez firmę OTEC, elementy, takie jak dyski turbiny i łopatki turbiny lub sprężarki, są mocowane w uchwycie i zanurzane w obrotowym
pojemniku wypełnionym wsadem (mediami) ściernym lub polerującym. Przedmioty obrabiane można również obracać lub ustawiać pod określonymi kątami w przepływającym wsadzie.
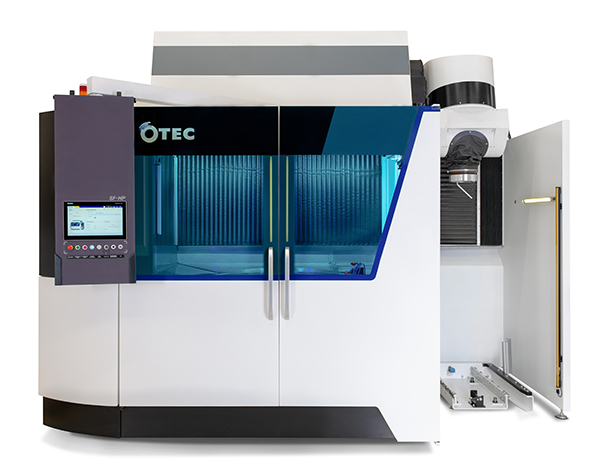
Względny ruch między wyrobem a wsadem zapewnia równomierne wykończenie. Ogromne siły nacisku do 9 ton powstające podczas obróbki strumieniowej mogą usuwać materiał szybciej i dokładniej niż jakikolwiek inny rodzaj obróbki wykńczeniowej powierzchni:
w zależności od wielkości komponentu, stanu początkowego i przygotowania (np. wstępne fazowanie) można uzyskać promień do 700 µm w ciągu 15 minut. A ponieważ granulki wsadu są tak drobne, proces zaokrąglania nadaje się również do skomplikowanych, trudno dostępnych geometrii.
OTEC jest jedynym dostawcą polerek strumieniowych ze zintegrowaną automatyzacją do dużych i ciężkich elementów: nowo opracowany SF-HP przeznaczony jest do obróbki wyrobów o średnicy do 650 mm i wadze do 200 kg.
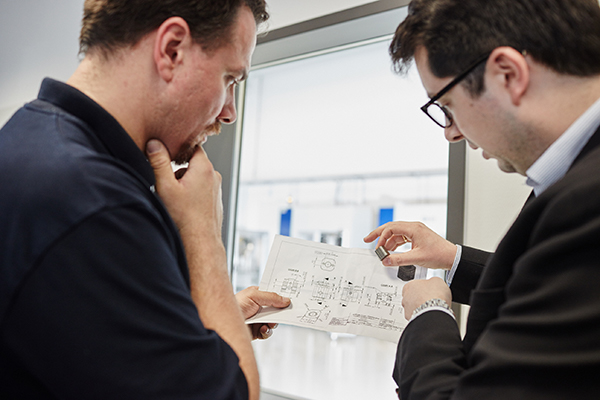
OPRACUJ SWÓJ PROCES OBRÓBKI WYKOŃCZENMIOWEJ Z POMOCĄ EKSPERTÓW OTEC PRÄZISIONSFINISH
Technologia obróbki strumieniowej OTEC jest doskonałym wyborem dla komponentów o podobnych wymaganiach w zakresie obróbki wykończeniowej. Przykłady obejmują łopatki turbin i sprężarek, zamki łopatek turbin, bliski, serwozawory, koła zębate, nakrętki śrub kulowych i elementy podwozia. Nasz zespół specjalistów w OTEC Finishing Center jest gotowy do pomocy w opracowaniu procesu — niezależnie od geometrii, jakości powierzchni lub wymagań dotyczących zaokrąglenia. Współpracuj z nami, aby zidentyfikować dokładnie właściwy proces dla Twojego wyrobu. Umów się na spotkanie już dziś, aby zobaczyć, jak Twój wyrób jest obrabiany, osobiście lub przez internet.
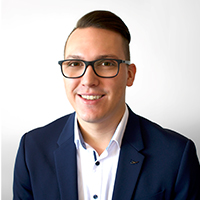
KONTAKT DO SPECIALISTY AEROSPACE
Adrian Kofler (M.Eng.)
+ 49 (0) 70 82 - 49 11 20
a.kofler@otec.de