Automated cutting edge optimisation of stamping and forming tools
Tools Success Story
The challenge facing the OTEC team of experts was to find an automated solution that delivers consistently high-precision results for the stamping and forming machines of the renowned machine manufacturer Bihler. Optimum cutting edge rounding and a high-gloss polish on surfaces of the most varied tools made of hard metal or hardened steel are achieved in just one step using the OTEC machines. This ensures the long service life of tools and significantly reduces production costs.
Consistent high performance quality with measurable success
For the tool industry, achieving the best possible product quality and increasing efficiency in the manufacture of stamping and bending parts are crucial for maintaining a competitive edge in the market. For the success story of Otto Bihler Maschinenfabrik, in particular, this means optimal cutting edge rounding of 10-20 µm and a high-gloss polish on the outer surfaces with a surface roughness of up to Ra 0.02 µm for cutting punches and dies.
This high performance quality means that even with a higher cycle time, the hard metal or hardened steel tools achieve consistently and reliably precise results and a maximum service life. Using the latest 3D measuring technology from Keyence, the quality is also constantly and reliably checked and documented.
Precise process flexibility using an automated Stream Finishing solution
A customised process designed to fully meet the exacting surface requirements was developed in the OTEC Finishing Center. The requested roughness parameters for the stamping and forming tools were achieved by means of mass finishing technology using what is called the Stream Finishing Process.
With the SF technology, workpieces are clamped in a holder and lowered into a rotating container filled with an abrasive or polishing medium. The granulate-type abrasive circulates around the workpieces, thereby ensuring even, homogeneous abrasion. By adjusting the processing parameters and the type of abrasive
A special cycle mode in the machine means that this process is also suitable for the most varied tool geometries. The angle of the clamped tool is repeatedly changed automatically during the process so that the most varied surfaces can be specifically targeted. Thanks to the optimised processing of the tools in the Stream Finishing Unit, manual process steps (tasks) are no longer required. The innovative solution is reliable and delivers consistent results without fluctuations
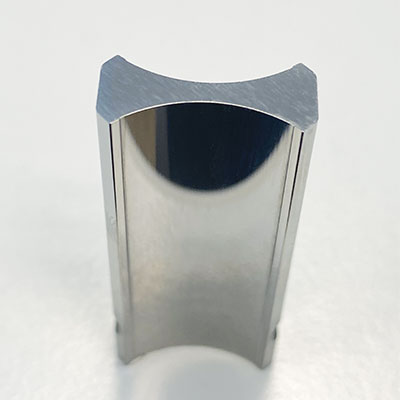
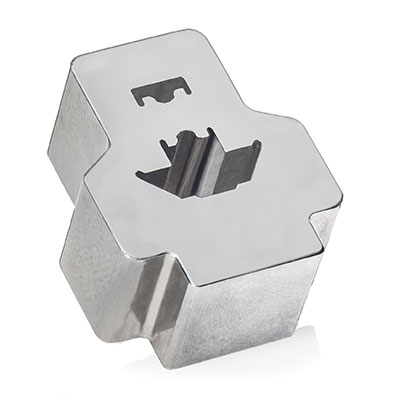
Hand-in-hand: Implementation of the process for the customer
The successful interaction between machine size and equipment, abrasive and the correct process parameters was determined as a process using tools used in series production by the customer and then tested in real use. Following installation of the OTEC SF-1 with intermittent drive, the unit was successfully commissioned at Bihler with the help of the OTEC specialists. Continued support from Process Development and After-Sales will guarantee excellent process reliability and efficient use of the unit on a long-term basis.
Benefits of OTEC surface processing
- Surface roughness parameters are significantly reduced
- Flexible processes for the most varied requirements for tools
- Fast processing
- No fluctuations in quality as a result of automation
- Durable high-quality products and increased productivity
- Precise processing of workpieces of the most varied geometries
- Automation delivers consistently high-gloss results
- Increased productivity thanks to longer tool service life
- Reliable quality control
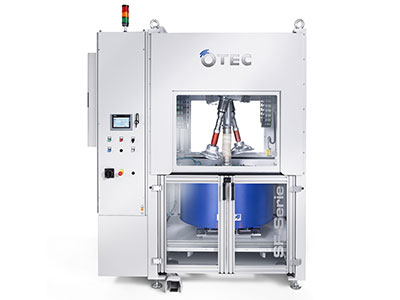
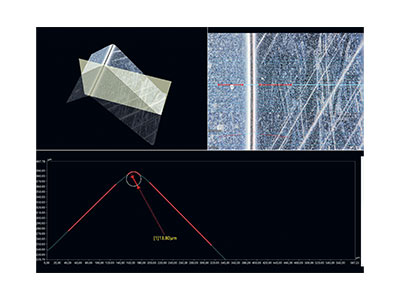
The surface is now the top performer
The use of the OTEC Stream Finishing Units leads to effective resource and cost savings while at the same time achieving the required surface roughness parameters and surface properties. The extremely high demands of hard metal tools in terms of consistently high product quality and increased effectiveness in production are reliably met and the service life of the parts is increased significantly while at the same time reducing maintenance costs.
The special property of the mass finished surface topography with its significant reduction in roughness peaks allows excellent performance of the tools. Smoothing and polishing of the surfaces reduces friction and thus the thermal load. This significantly reduces wear on the tools and prepares the surface perfectly for a coating
“The technical aspects of the OTEC solutions have surpassed our expectations. The precision and efficiency of processing have really boosted our production”, , says Klaus Wiesmath, Technical Director, enthusiastically.
Example of surface measurements of tools
Comparison of surface topographies
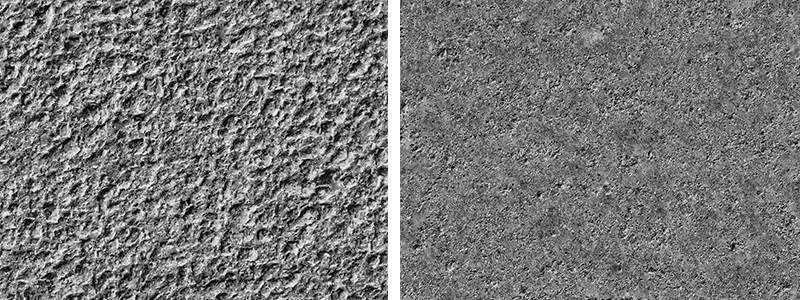
“Our collaboration with OTEC was excellent. Our specific requirements were fully taken into account.They supported us step by step through the process”. Head of Plant Engineering Heinrich Etschmann is entirely satisfied.
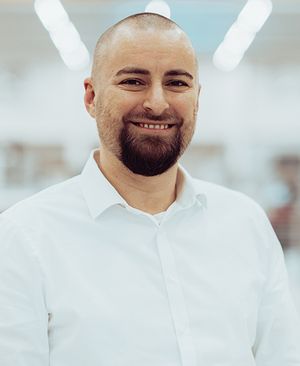
"OTEC is your reliable partner when it comes to perfection in the tooling sector."
Your contact for innovative surface processing
“The growing pressure in the tools market due to the increasing competitiveness of emerging countries requires intensive cooperation when it comes to finding a solution in order to achieve a perfect result. Always being one step ahead, being there for our customers, by continually optimising our processes – that is the philosophy at OTEC.
The OTEC Finishing Center develops a process specially tailored to your workpiece and your application. You too should start with our customised process development.”
Steffen Permann (Area Sales Manager).