Industria automobilistica: FINITURA SUPERFICIALE MIRATA? VANTAGGI TANGIBILI!
Intervista
Da qualche tempo la stampa riporta che l'UE prevede di introdurre sanzioni per l'industria automobilistica a partire dal 2020. Il costruttore dovrà pagare 95 euro a Bruxelles per ciascun veicolo di nuova immatricolazione con un motore a combustione interna e per ogni grammo che supererà il limite di CO2 di 95 g/km. Secondo il Consiglio Internazionale dei Trasporti Puliti (ICCT) nel 2018 le emissioni sono state in media di 121 g/km.
Florian Reinle, ingegnere del dipartimento di Ricerca e Sviluppo dell'azienda OTEC, ci spiega come le case automobilistiche possano ottimizzare ulteriormente i loro processi di produzione riducendo l'attrito dei loro componenti.
Signor Reinle, Lei si occupa del tema dell'attrito presso OTEC e quindi sa bene quale sia il tallone d'Achille dell'industria automobilistica. Secondo Lei, come è necessario comportarsi?
"Dalla nostra esperienza e dal confronto con i clienti abbiamo imparato che esiste una stretta connessione tra efficienza e finitura mirata e ottimizzata delle superfici di attrito. I componenti con attrito, quali pezzi di camma, segmenti di pistoni, alberi a gomito o ingranaggi, possono essere levigati con precisione anche meccanicamente. Dal momento che alla levigatura uniamo ulteriori vantaggi, come ad esempio la sbavatura, si tratta a tutti gli effetti di un miglioramento a 360°".
Sembra un tema impegnativo e allo stesso tempo stimolante. Potrebbe prima spiegarci cosa intende per finitura mirata della superficie?
"Certo! Con questo termine si identificano una serie di operazioni fondamentali: il livellamento della superficie, la rimozione dei picchi di rugosità e la lavorazione delle scanalature. Ciò si traduce in una superficie isotropica e un livello di rugosità concordato con il cliente.
Con il nostro processo, prepariamo il componente all'uso sul campo con un elevato apporto di energia di attrito. Ci prendiamo cura sia dell'attrito che della riduzione dell'usura. Sulla superficie si crea uno strato di taglio in cui produciamo cambiamenti strutturali e pressione residua, ottimizzando così il componente per l'uso.
Oltre a ciò, una finitura così precisa riduce l'attrito nella trasmissione: si consuma meno carburante, ovvero l'energia di propulsione fornita viene utilizzata in modo più efficace e anche le emissioni di CO2 vengono ridotte".
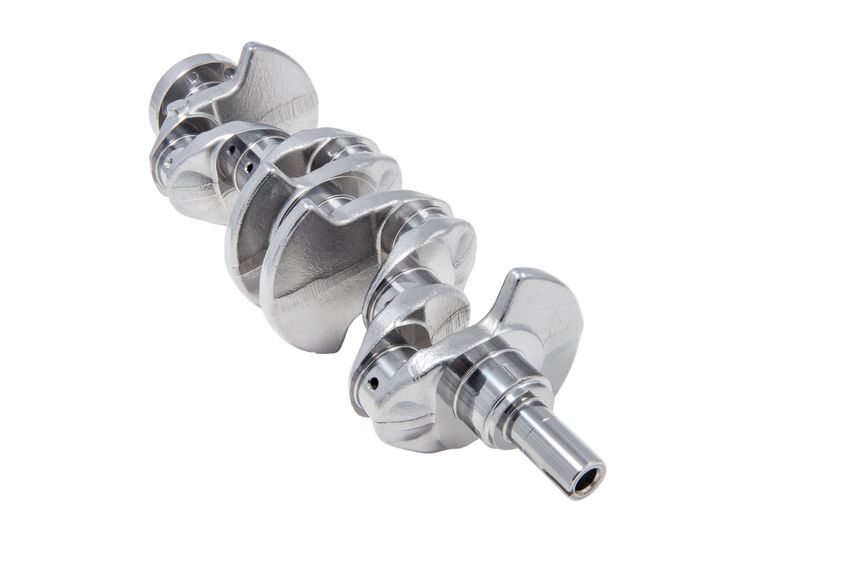
Sembra molto promettente: può parlarci degli altri vantaggi concreti e spiegare quali sono le migliorie apportate ai componenti?
"Grazie alla lavorazione meccanica possiamo assicurare la massima affidabilità di processo e, naturalmente, la ripetibilità dello stesso con tempi notevolmente ridotti, diminuendo così anche i costi. E la qualità del prodotto, invece, è l’unica cosa che aumenta. Osservando il componente lo si nota subito, ad occhio nudo. Se prendiamo in considerazione la sbavatura o l'arrotondamento mirato dei bordi, avremo anche ulteriori vantaggi tangibili. È evidente che la maneggevolezza sarà migliorata e che l'assemblaggio "scorrerà" meglio - nel senso letterale del termine - quando si premeranno i componenti o si inseriranno elementi sensibili come le guarnizioni.
Nel caso di parti soggette ad elevati livelli di attrito e usura, si applicano spesso dei rivestimenti: questi ultimi aderiranno meglio e in maniera più stabile se la superficie sarà stata precedentemente ottimizzata. Naturalmente sarà anche possibile levigare il pezzo dopo il rivestimento.
Un altro effetto interessante è il possibile miglioramento del comportamento di NVH (rumori, vibrazioni e ruvidezza). In altre parole, le vibrazioni udibili o percepibili saranno ridotte.
E proprio come il comportamento di NVH va oltre il singolo componente, levigando la superficie potremo avviare importanti effetti sinergici. Ad esempio, con l'uso di lubrificanti a bassa viscosità per una maggiore efficienza dell'intero sistema".
Ora si legge sulla stampa che l'e-mobility è senza dubbio la soluzione per i produttori di veicoli per evitare o limitare le sanzioni.
"Sì, le condizioni quadro politiche richiedono che si introducano sul mercato un numero sempre maggiore di veicoli elettrici. Ciò influisce sulle diverse classi di veicoli in misura diversa. Tuttavia, le relazioni si basano principalmente sul fatto che vengono fabbricati veicoli a propulsione elettrica.
La sola produzione non è sufficiente: i veicoli, dopo, devono scendere in strada. Ed è qui che entrano in gioco concorrenza e consumatori. Se un cliente finale è interessato all'acquisto di un'automobile elettrica, un fattore importante è il rapporto costi-benefici. In questo caso sono fondamentali l'autonomia, le spese di gestione e il costo d'acquisto".
Anche nel caso della mobilità elettrica attrito e NVH svolgono un ruolo importante, signor Reinle?
“Il trattamento superficiale dei componenti degli ingranaggi offre vantaggi tangibili che sono estremamente rilevanti per il cliente finale: si potrebbe dire che, a tutti gli effetti, valgono oro. Come per il motore a combustione interna, l'efficienza viene aumentata ottimizzando la superficie dei componenti e si ottiene un miglioramento complessivo delle proprietà dei pezzi. Inoltre, il processo - già efficiente in termini di costi - può essere convogliato su un piccolo numero di componenti responsabili delle perdite di attrito. Alla fine si ottiene la stessa autonomia con una batteria più piccola, quindi più economica, o più autonomia con la stessa batteria.
E le emissioni di rumore, ovvero l'ottimizzazione NVH, rappresentano un altro argomento importante nello sviluppo di motori elettrici, dal momento che adesso si sentono anche quei rumori che il motore a combustione interna precedentemente copriva".
Perché i produttori di automobili dovrebbero ricorrere proprio all'uso della tecnologia di processo OTEC? Qual è il vantaggio di processo?
"Per i clienti del settore automobilistico che già fanno affidamento sulla finitura di precisione OTEC, oltre ai vantaggi già noti relativi ai componenti si aggiungono quelli di processo. Lo speciale metodo di finitura a flusso abrasivo di OTEC è un processo privo di acidi, sicuro per le persone e per l'ambiente. Senza dimenticare che è anche più economico rispetto ad altri processi di finitura. E con tempi di processo di 90 secondi in media, è il processo di finitura vibratoria più veloce.
Le differenze rispetto alle altre tecnologie in questo settore sono le elevate forze di lavorazione e l'alta percentuale di energia di attrito nella macchina. Con questo metodo i pezzi vengono bloccati al supporto e immersi nel contenitore rotante riempito con agenti abrasivi o lucidanti.
L'effettivo movimento di lavorazione è dato sia dal flusso rotatorio del materiale di levigatura o lucidatura sia dalla rotazione del pezzo. Ciò significa che la rimozione può essere eseguita in modo più preciso e rapido rispetto a qualsiasi altra rettificatrice per superfici. La serie SF è stato appositamente sviluppata per applicazioni per le quali finora non c'erano processi soddisfacenti. I requisiti di ripetibilità e velocità sono fattori decisivi cui l'industria automobilistica non può rinunciare.
Grazie alle elevate forze di processo, è possibile lavorare geometrie fini con abrasivi leviganti e lucidanti delicati senza rinunciare alla massima efficacia. L'integrazione nella produzione in linea è molto semplice grazie alla possibilità di regolare i tempi di ciclo e grazie al caricamento automatico. "
Grazie mille, signor Reinle!
Funziona come un orologio ed è tutto automatizzato: SF con sistema di carica-mento robotizzato (RLS)
Quando si lavora una grande quantità di pezzi, poter ridurre i tempi di caricamento e d'impostazione influisce notevolmente sull’efficienza generale della lavorazione. Tutto ciò è possibile grazie al sistema di caricamento automatico del robot (SF RLS, v. figura a sinistra).
Su richiesta le macchine della serie SF Automation possono essere equipaggiate con il sistema PULSFINISH e sono ideali, tra le altre cose, per la produzione in linea. A seconda del profilo richiesto, le macchine sono pre-equipaggiate per il caricamento automatico o – opzionalmente – prevedono il caricamento automatico già integrato.
Il design modulare della macchina consente un facile adattamento al tempo del ciclo. La SF Automation può quindi essere facilmente integrata in una linea di produzione.
Lavorazione gratuita di un campione
Metteteci alla prova, inviateci il vostro campione! Nel nostro centro di finitura interno saremo in grado di determinare il processo di lavorazione ideale per le vostre esigenze. Maggiori informazioni qui: