SUPERFICI DI PEZZI PRODOTTI CON PROCESSO ADDITIVO: LAVORAZIONE EFFICACE GRAZIE ALLA FINITURA A DISCO
La DIN8580 definisce la stampa 3D come un processo di deformazione grazie al quale da un materiale informe si genera un corpo solido con una forma geometricamente definita. Si utilizzano a tal fine materiali diversi come metallo, plastica o ceramica. I processi di produzione additiva hanno ormai raggiunto un buon livello di maturità da quando sono stati inventati oltre 30 anni fa, tanto che si sono gradualmente affermati nella produzione industriale. Che si tratti di prototipi o produzione in serie, l'uso di processi di produzione additiva per componenti visibili e funzionali o prodotti di design personalizzati è oramai intersettoriale. Alcuni esempi di applicazione sono gioielli, protesi dentali e auricolari.
Con le crescenti possibilità offerte dalla produzione additiva, aumentano anche le esigenze dei pezzi in lavorazione: la qualità della serie deve essere raggiunta in termini di finitura della superficie, ripetibilità e affidabilità del processo.
Le parti prodotte in modo additivo rappresentano una sfida speciale per chi si occupa di finitura superficiale
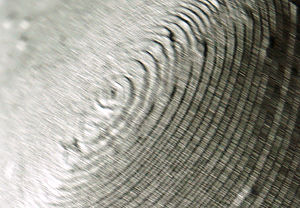
In tutti i processi di stampa 3D, i diversi livelli del pezzo vengono prodotti in modo selettivo. Il componente risulta quindi costituito da una serie di strati. Il principio del processo assicura flessibilità e individualità nella definizione dei componenti. A causa della struttura a strati, le parti prodotte in modo additivo hanno una struttura superficiale singolare, caratterizzata da scanalature, pori, crepe e cavità.
Tre approcci classici per migliorare la qualità della superficie e ridurre l'effetto "a strati".
La finitura manuale, quella con solventi e la levigatura, ad esempio in un vibratore, sono considerate soluzioni classiche.
Lo svantaggio di levigatura e lucidatura manuali è che, a causa del fattore umano, la ripetibilità e i tempi di processo non consentono una produzione economica. Nella lisciatura chimica, i solventi devono essere processati, cambiati e smaltiti in modo laborioso e quindi costoso. Inoltre, i costi di acquisto sono più elevati rispetto ad altri metodi di finitura, che, nel loro insieme, ostacolano l'obiettivo di una produzione in serie efficiente. Per la levigatura, invece, non vengono utilizzati prodotti chimici ma i tempi di processo sono molto lunghi e spesso non economici.
Esiste una soluzione alternativa per la finitura efficace di parti prodotte in modo additivo da materiali diversi e in serie? Sì, c’è!
I sistemi a disco centrifugo OTEC creano superfici omogenee in tempi brevissimi e senza prodotti chimici
Le superfici a spugna, a poro aperto, possono essere omogeneizzate - ovvero levigate e lucidate - nei sistemi a disco centrifugo OTEC in tempi incredibilmente rapidi.
Ciò è reso possibile dall’automatizzazione dell’intero processo: pezzi delle dimensioni di un pugno o più piccoli (a seconda della versione della macchina) vengono inseriti nel buratto blu come pezzi sfusi oppure singolarmente insieme ad agenti di levigatura e lucidatura adattati alla geometria e al materiale del pezzo. Il fondo del contenitore è a forma di disco e montato in modo tale che possa girare.
Grazie al movimento rotatorio del disco nel contenitore rigido, gli agenti di lavorazione e i pezzi si trovano immersi in un flusso toroidale. La lavorazione dei pezzi che ne deriva è molto intensa ed esclusivamente meccanica.
Spesso imitato - mai eguagliato: la serie CF è sinonimo di flessibilità, ripetibilità e affidabilità
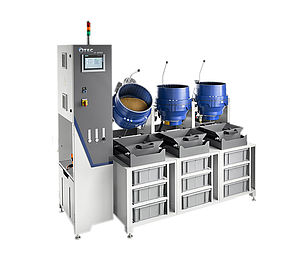
- Nel sistema di controllo centrale dell'impianto, i parametri di processo del pezzo in lavorazione vengono memorizzati, monitorati ed eseguiti con la semplice pressione di un pulsante. In questo modo sono sempre garantiti parametri di processo costanti. La concentrazione di acqua/composto è regolabile tramite pannello touch, garantendo così la sicurezza del processo.
- Tecnologia sofisticata e intelligente: il contenitore è costituito da una base a forma di disco, un cilindro con struttura scanalata e un anello di usura sostituibile. Ciò significa che in caso di usura non deve essere sostituito l'intero buratto, riducendo così al minimo i costi di sostituzione.
- Grazie al sistema zero gap sviluppato da OTEC, né i pezzi - anche se molto sottili - né il granulato di processo rischia di rimanere impigliato nell'intercapedine durante il processo di lavorazione. Inoltre, non ci sono residui d'acqua nel serbatoio di lavoro alla fine del processo in quanto l'acqua può defluire completamente.
- Grazie alla forma ottimale del contenitore, la macchina garantisce un'ottima circolazione. L'utente che usa la serie CF di OTEC può beneficiare di tempi di processo ridotti e di superfici più lisce.
Il tempo è denaro!
- Rispetto alla rettifica vibratoria, i produttori di parti realizzate con processo additivo beneficiano di tempi di lavorazione da 5 a 10 volte più brevi quando utilizzano i sistemi a disco centrifugo di OTEC. Una velocità di rimozione meccanica maggiore agisce positivamente sulla superficie e riduce significativamente il tempo di lavorazione.
- Contrariamente alla lisciatura chimica, non vengono utilizzati prodotti chimici aggressivi come solventi. Inoltre, la gestione dei sistemi CF è sicura, i processi di lavoro più facili e rapidi. Da non sottovalutare che i costi di acquisizione e operativi di un sistema a disco centrifugo sono inferiori rispetto alle altre tecniche. In sintesi, il costo unitario della produzione in serie è notevolmente ridotto con la serie CF.
- La lavorazione manuale è ridotta al minimo o addirittura del tutto eliminata. Ciò dipende fortemente dalle esigenze di applicazione e di elaborazione. Di norma, l'80% degli sforzi manuali viene eliminato grazie alla lavorazione ripetibile e affidabile del processo a disco centrifugo. Solo il tocco finale, ad esempio nel settore della gioielleria, viene ancora eseguito manualmente.
Esempio di lavorazione CF: pezzi in metallo realizzati in SLS
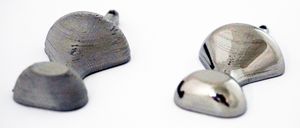
I test di lavorazione con pezzi in metallo stampati utilizzando il processo SLS nelle macchine a disco centrifugo di OTEC durano mediamente da 1 a 2 ore per lotto.
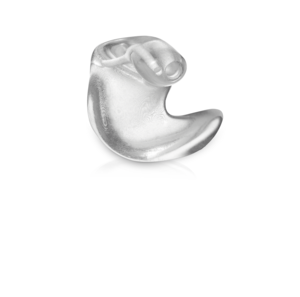
Esempio di finitura CF: auricolari in plastica stampati in 3D
La scelta della macchina, del materiale e della durata di processo varia in base al numero di componenti e a come questi si presentano all'inizio. Il tempo di lavorazione è mediamente di 1-2 ore per ogni fase di processo. Con determinati tipi di macchine è possibile lavorare in un unico ciclo anche quantità rilevanti. La serie CF di OTEC è la scelta migliore sia per le serie limitate sia per la produzione a ciclo continuo.
SEPARA IL PEZZO DA LAVORARE E IL FLUIDO DI PROCESSO: VAGLIATRICE MOBILE UNISEPA - COMPATTA E FLESSIBILE!
La nuova UNISEPA di OTEC è una soluzione universalmente applicabile per la separazione di pezzi e materiali di lavorazione. Grazie alle opzioni di impostazione della valvola dosatrice, alla frequenza e alla velocità di vibrazione, l'UNISEPA svolge quasi tutte le attività di separazione in maniera completamente automatizzata.
Video CF 1x18 con Unisepa (Youtube)
Ogni pezzo è diverso: mettici alla prova!
Inviaci il tuo pezzo di prova e definiremo il miglior processo di lavorazione per le tue esigenze grazie ai nostri esperti nel nostro centro di finitura interno.