Environmentally friendly surface optimisation for drive shafts in electric trucks
Automotive Success Story
Functional reliability, cost-effectiveness and the use of environmentally friendly technology were the particular challenges for processing electric drive shafts from a well-known Polish automotive supplier. With OTEC machines, optimal surface tolerances are achieved on parts for electric high-speed drives where absolute functional reliability is of the greatest importance.
Function-relevant surface tolerances
The automotive supplier and renowned drive specialist was looking for an efficient, cost-saving and above all reliable solution for optimising the surfaces of drive shafts in electric trucks. To guarantee the critically important functional reliability, exact surface roughness parameters had to be adhered to. The increasing demand for electric trucks is giving rise to high quantities in production and thus requires a high level of automation during processing and handling. It was also necessary to find an optimal solution in order to take into account an already tight timeframe.
Customised Stream Finishing solutionA customised
process designed to fully meet the exacting surface requirements was developed in the OTEC Finishing Center. The requested roughness parameters for the drive shafts were achieved by means of mass finishing technology using what is called the Stream Finishing Process.
With the SF Technology, workpieces are clamped in a holder and lowered into a rotating container filled with an abrasive or polishing medium. The granulate-type abrasive circulates around the workpieces, thereby ensuring even, homogeneous abrasion. By adjusting the processing parameters and the type of abrasive used, both highly abrasive and fine polishing processes can be performed with just one machine.
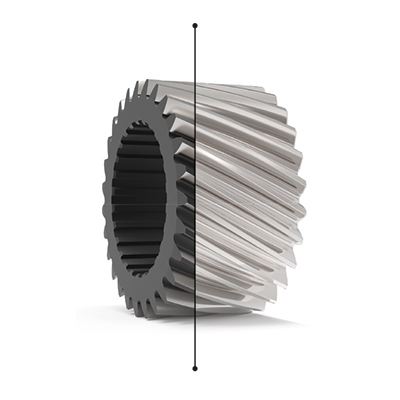
Customised automation technology
The solution for this particular requirement from the e-mobility sector is suitable for series production and was achieved using a SF Machine with 3 spindles which can automatically process 3 workpieces at the same time.
Benefits of OTEC surface processing
- Narrow tolerances of multiple surface roughness parameters are met
- Isotropic surface topography
- Fast processing of 3 workpieces in less than 5 minutes
- The process-related introduction of internal compressive stresses eliminates the need for a subsequent blasting procedure
- Easy automation and integration in the production line
The use of a waste water centrifuge and the corresponding recirculation system means that the OTEC solution is environmentally friendly and saves resources. Over 95% of the costs for fresh water and waste water disposal can be saved using the centrifugal water recirculation system.
- Up to 3 workpieces can be processed at the same time
- Fully automated workpiece removal and return
- Sustainable process without the use of aggressive abrasives
Flexible and competent
In order to be able to manufacture and deliver drive shafts during the machine setup time, the customer’s start of production was supported by OTEC-internal subcontracting. Following the successful setup and testing of the Stream Finishing Machine, the unit was integrated fully into the automotive supplier’s production process. Continued support from OTEC Process Development and OTEC After-Sales will guarantee excellent process reliability and efficient use of the unit on a long-term basis.
The surface is now the top performer
The use of the OTEC Stream Finishing Unit leads to effective resource and cost savings, while at the same time achieving the required surface roughness parameters and surface properties. The extremely high technical demands of high-speed electric drives in terms of optimal functioning and resilience are reliably met and the service life of the parts is increased significantly, while at the same time reducing maintenance costs.
The particular properties of the mass-finished surface topography with its pronounced isotropy and the internal compressive stresses that are introduced make the drive shafts top performers.
Example of surface measurements of drive shafts
Comparable surface profile, measured with Alicona G6 80WD4
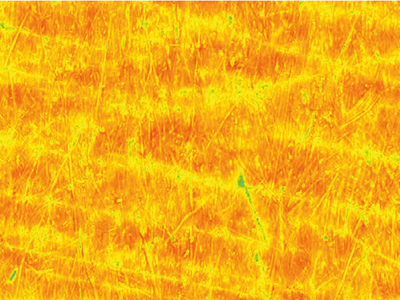
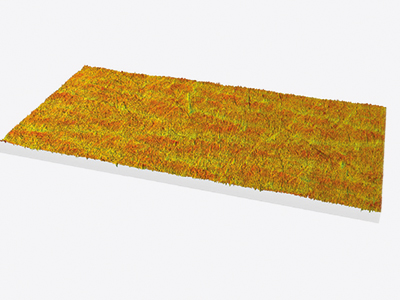
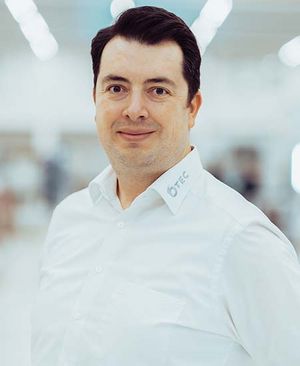
"OTEC is your reliable partner for innovative solutions in the automotive industry."
Your contact for innovative surface processing
“The rapid technical development in the automotive industry requires intensive cooperation when it comes to finding a solution in order to achieve a perfect result. Always being one step ahead, being there for our customers, by continually optimising our processes – that is the philosophy at OTEC.
The OTEC Finishing Center develops a process specially tailored to your workpiece and your application. You too should start with our customised process development.” Nicolas Petri (Head of Sales Germany).