POLISSAGE À FLUX CONTINU – LA SOLUTION ÉCOLOGIQUE POUR REMPLACER LES PROCÉDÉS ACCÉLÉRÉS PAR VOIE CHIMIQUE
TRIBOFINITION : LES ENGRENAGES SOUMIS À FORTES CHARGES DANS L’INDUSTRIE AÉRONAUTIQUE
Il existe plusieurs méthodes et différents procédés pour la reprise des-composants métalliques de fabrication industrielle. Ils ont tous leurs avantages et leurs inconvénients en termes de taille, de géométrie, de matériau et de difficulté d’usinage. Nous comparerons quatre procédés établis sur le marché selon les critères santé, environnement et rentabilité en partant de l’exemple d’une roue dentée.
UN ENGRENAGE – DE MULTIPLES DÉFIS POUR LE TRAITEMENT
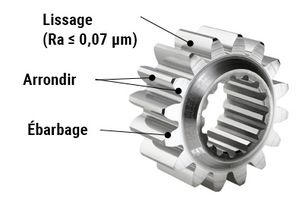
Pour les applications dans le domaine de l’industrie aéronautique, les engrenages en acier soumis à fortes charges sont souvent rectifiés avec une extrême précision et trempés à un degré élevé (> 60 HRC). Leur surface est dure et ferme. Pour qu’ils puissent remplir leur fonction avec une parfaite fiabilité, il est indispensable que leur surface présente une structure irréprochable et soit parfaitement isotrope, c’est-à-dire extrêmement uniforme dans plusieurs directions. Outre le lissage à des valeurs parfois inférieures à Ra 0,1 µm, les surfaces de développante ne doivent pas faire apparaître d’ondulations ni de rainures de meulage. De plus, les bords sur les côtés et sur le sommet de la dent doivent présenter un rayonnage homogène.
TOUS LES TRAITEMENTS NE SE VALENT PAS
Maintenant que le cahier des charges est bien défini – la question est de savoir comment atteindre au mieux l’objectif.
Une première possibilité consiste à procéder au lissage et rayonnage de façon manuelle ou mécanique, guidée par un robot. Il convient toutefois de noter que la qualité de l’usinage ne reste pas constante tout au long du cycle de vie de l’outil. En effet, le traitement de surface obtenu devient de plus en plus imprécis au fil du temps en raison de l’usure progressive de la meule ou de la brosse.
Pour l’usinage de géométries intérieures, les deux procédés produisent l’un comme l’autre des résultats très inégaux, car les outils ne parviennent pas bien à s’adapter au composant et le positionnement dans des géométries étroites est souvent difficile, voire impossible. Ces méthodes parviennent définitivement à leurs limites sur les composants ayant des tolérances très faibles et n’entrent donc pas en ligne de compte.
Le traitement dans un vibrateur à auge est souvent utilisé et correspond à l’état de l’art actuel. L’utilisation de certains fluides de traitement acides raccourcit le temps de traitement. Ces fluides de traitement peuvent notamment inclure des mélanges de sel de phosphate, d’acide phosphorique, d’acide oxalique, d’oxalate de sodium, de sulfate, de bicarbonate de sodium, de chromate, de chromate de sodium, d’acide chromique et d’acide sulfurique.
La plupart de ces substances sont des marchandises dangereuses et requièrent une attention particulière lors de leur manipulation. Le chromate (de sodium) et l’acide chromique sont enregistrés dans le cadre du règlement REACH (enregistrement, évaluation et autorisation des produits chimiques) comme substances extrêmement préoccupantes : cancérogènes, mutagènes et toxiques pour la reproduction (chromate de sodium).
L’acide sulfurique, l’acide oxalique et l’acide phosphorique, ainsi que les substances déjà mentionnées que sont le chromate de sodium et l’acide chromique, sont considérés comme corrosifs et partiellement toxiques. C’est pourquoi la plupart de ces substances sont classées comme suit selon l’étiquetage des substances dangereuses du SGH :
- toxicité aiguë
- danger pour le milieu aquatique
- divers risques pour la santé
- corrosif pour les métaux, corrosif pour la peau, graves lésions des yeux
Le procédé répond aux exigences en termes de tâche de traitement, mais le fluide ne peut généralement être utilisé qu’une seule fois et doit être remplacé à la fin du processus. L’approvisionnement, la neutralisation et l’élimination entraînent des coûts élevés, ce qui en réduit la rentabilité économique. L’utilisation de substances dangereuses présente également des risques pour la santé humaine et l’environnement, comme indiqué précédemment.
On trouve également sur le marché des procédés d’électropolissage permettant de polir des pièces métalliques en une seule passe. Ils fonctionnent avec de l’électrolyte de sorte que même les géométries internes peuvent être atteintes et traitées.
L’un des principaux inconvénients de ce procédé est que l’ondulation inhérente au processus de meulage pour formage ne peut pas être éliminée lors de l’électropolissage – la performance d’enlèvement est tout simplement trop faible. La durée de traitement moyenne peut aller de 30 minutes à plusieurs heures. En outre, avec ce procédé, seules les zones exposées sont traitées avec intensité. Après une période d’utilisation déterminée, de l’électrolyte doit également être éliminé dans la catégorie des déchets dangereux et il faut acheter un nouveau produit coûteux
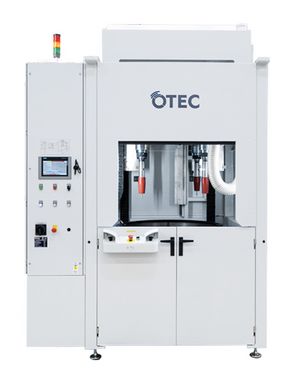
POLISSAGE À FLUX CONTINU – LA SOLUTION ÉCOLOGIQUE
Pour commencer, précisons que le polissage à flux continu donne des résultats comparables à ceux de la tribofinition accélérée par voie chimique. Cependant, il fait appel à un traitement exclusivement mécanique et ne nécessite pas l’utilisation de granulat d’acide ou d’électrolyte, ce qui augmente la rentabilité du processus de reprise.
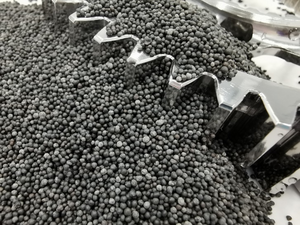
POURQUOI LE POLISSAGE À FLUX CONTINU MARCHE-T-IL?
Ce procédé mis au point par OTEC consiste à fixer les pièces dans un support avant de les plonger dans une cuve en rotation remplie d’abrasifs ou d’agents de polissage. Grâce à la rotation supplémentaire de la pièce et au mouvement relatif qui en résulte entre la pièce et le support, on obtient un traitement homogène, sans aucun travail manuel. Sur des géométries complexes, il est possible d’obtenir des surfaces de haute précision avec des rugosités allant jusqu’à Ra 0,01 µm.
Grâce aux forces de traitement appliquées, l’enlèvement de matière est plus ciblé et plus rapide qu’avec n’importe quel autre traitement de surface. Les produits de traitement fins atteignent les géométries internes et les traitent sans aucun problème.
COMME UNE HORLOGE : DES ENGRENAGES RÉSISTANTS À L’USURE GRÂCE AU POLISSAGE À FLUX CONTINU
Un film lubrifiant réduit la friction et l’usure au niveau de l’interaction entre les engrenages. Dans le cas du polissage à flux continu, des poches de lubrification de taille microscopique se forment à la surface – le lubrifiant est déposé dans ces poches, ce qui représente un avantage en faveur de ce procédé. En effet, si la surface est trop plate et trop lisse, il risque d’y avoir une rupture du film lubrifiant entre les dents en contact, ce qui provoquerait le grippage de l’engrenage et sa défaillance totale.
Le polissage à flux continu apporte un bénéfice global aux engrenages. Il entraîne en effet un nivellement de la surface ainsi que la suppression des pics de rugosité ou des rainures de traitement. On obtient ainsi une surface isotrope et une rugosité ciblée, décidée d’un commun accord avec le client.
Les engrenages traités par le polissage à flux continu sont préparés à l’utilisation ultérieure (« rodage ») grâce à un apport important d’énergie de friction. En plus de réduire la friction et l’usure, le procédé a pour avantage de former une couche de cisaillement à la surface. Il entraîne ainsi des modifications structurelles et des contraintes résiduelles de compression dans cette couche, qui conditionnent l’engrenage de manière favorable.
Le polissage à flux continu apporte un bénéfice global aux engrenages. Il entraîne en effet un nivellement de la surface ainsi que la suppression des pics de rugosité ou des rainures de traitement. On obtient ainsi une surface isotrope et une rugosité ciblée, décidée d’un commun accord avec le client.
Les engrenages traités par le polissage à flux continu sont préparés à l’utilisation ultérieure (« rodage ») grâce à un apport important d’énergie de friction. En plus de réduire la friction et l’usure, le procédé a pour avantage de former une couche de cisaillement à la surface. Il entraîne ainsi des modifications structurelles et des contraintes résiduelles de compression dans cette couche, qui conditionnent l’engrenage de manière favorable.
LE POLISSAGE À FLUX CONTINU ÉVITE LES REBUTS
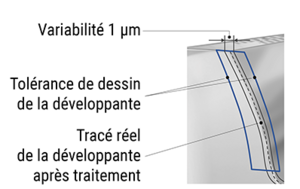
Le polissage à flux continu permet d’obtenir une variabilité de process extrêmement faible (seu-lement 1 µm), soit 5 à 10 fois moins par rapport aux procédés accélérés par voie chimique.
Il est ainsi possible d’éviter entièrement les rebuts résultant d’une variabilité élevée du processus de finition. Dans le cas des engrenages rectifiés de haute précision, cela se traduit par des économies à 5 chiffres – pour chaque pièce qui n’est pas mise au rebut.
EXEMPLE D’APPLICATION D’ENGRENAGES FORTEMENT SOLLICITÉS
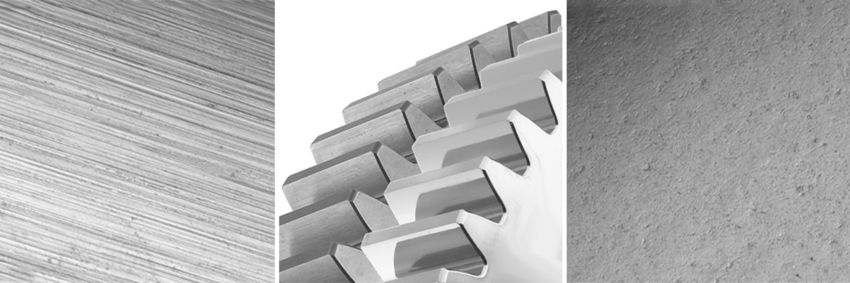
Avant traitement (à gauche) :
Ra 0.19 µm
Rz 1,358 µm
Rpk 0,418 µm
Après traitement (à droite) :
Ra 0,042 µm
Rz 0,551 µm
Rpk 0,139 µm
État initial
- Acier trempé, 60+ HRC, engrenage rectifié de haute précision
- Rugosité initiale : Ra of 0,19 – 0,21 µm
- Durée du process : 20-35 min
Résultat de traitement
- Surface extrêmement isotrope
- Rugosité finale : Ra 0,042 – 0,084 µm
- Suppression des entailles et des rainures
- Rayonnage homogène
- Variabilité extrêmement faible du process
- Introduction de poches de lubrification de taille microscopique à la surface
PROFITEZ DU POLISSAGE À FLUX CONTINU OTEC
- Ébarbage, rayonnage et lissage rapides et efficaces en une seule passe
- Variabilité extrêmement faible du process (1 µm) par rapport aux autres process existants (~5-10 µm)
- Fiabilité extrêmement élevée du process grâce à l’utilisation de mélanges opérationnels
- Surface extrêmement isotrope
- Pas de pics de rugosité (Rpk < 0,1 μm): moins d’usure, pas de rodage nécessaire, durée de vie de l’huile plus longue
- Faible risque de taches grises
- Procédé économique, car recyclable
- Pas d’élimination coûteuse des produits de traitement
- Pas de manipulation de produits chimiques dangereux
- Temps de traitement très courts – 4 fois plus rapides que le procédé accéléré par voie chimique
Le polissage à flux continu convient, entre autres, aux composants présentant des géométries complexes, un poids allant jusqu’à 200 kg et un diamètre allant jusqu’à 650 mm, tels que les disques de turbine, les aubes de turbine, les aubages, les servovalves ou les roues dentées pour le secteur aéronautique.
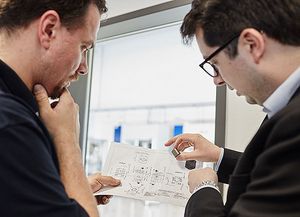
TROUVER LE BON PROCÉDÉ AVEC LES EXPERTS OTEC PRÄZISIONSFINISH
Quelles que soient la géométrie et les exigences relatives à la structure de la surface ou à la difficulté du traitement, l’équipe d’experts du Centre de finition d’OTEC vous aidera à trouver le bon procédé. Nous trouverons ensemble le process le mieux adapté à vos pièces. Prenez rendez-vous dès maintenant pour assister en direct à la création des surfaces parfaites sur vos pièces. Cliquez ici pour en savoir plus sur la définition individuelle du procédé.