INDUSTRIE ALIMENTAIRE : LES CONVOYEURS À VIS FONCTIONNENT MIEUX AVEC DES SURFACES UNIFORMÉMENT LISSES
Schaaf Technologie Gmbh mise sur le procédé OTEC de polissage à flux continu
Les convoyeurs à vis sont utilisés dans presque tous les domaines de l’industrie alimentaire. Ils sont fabriqués par tournage et fraisage à partir d’ébauches présentant les caractéristiques matérielles souhaitées. Le processus de fabrication s’accompagne malheureusement de rainures de fraisage et de surfaces rugueuses, ce qui détériore grandement la qualité du convoyage. C’est pourquoi les vis sont actuellement rectifiées et polies à la main au prix d’un travail fastidieux.
LISSAGE DES SURFACES RUGUEUSES ET RAYONNAGE DES ARÊTES
Les convoyeurs à vis sont utilisés pour des applications diverses. Ils permettent de déplacer des matières en vrac, mais aussi des masses visqueuses telles que des pâtes. On pourrait penser qu’une surface rugueuse est mieux à même de « saisir » et de transporter les produits. Mais c’est le contraire qui est vrai. Premièrement parce que les surfaces rugueuses favorisent le dépôt de résidus alimentaires et de microorganismes, ce qui rend le nettoyage de la surface beaucoup plus difficile. Deuxièmement parce que les arêtes vives et instables sont problématiques : à force d’être sollicitées, elles peuvent s’écailler, relâchant ainsi des fragments dans les denrées alimentaires. Pour éviter cela, il est indispensable d’avoir des surfaces lisses et homogènes dans les angles les plus réduits, ainsi que des arêtes rayonnées et stables ; c’est le seul moyen de garantir le processus de production et la pureté des aliments.
LE TRAITEMENT MANUEL EST COÛTEUX
Les pièces utilisées pour l’industrie alimentaire sont généralement traitées en plusieurs étapes de reprise. Dans la mesure du possible, on commence par lisser la surface avec une ponceuse à bande. Ensuite, les zones difficiles d’accès sont lissées manuellement et les bords sont rayonnés. Comme les convoyeurs à vis sont souvent lourds et peu maniables, ce processus manuel peut prendre plusieurs heures. De plus, le risque de blessure pour l’opérateur est élevé en raison des arêtes vives
DES SURFACES DE QUALITÉ À MOINDRE COÛT
Le moyen le plus efficace pour obtenir des surfaces uniformément lisses et des arêtes stables et arrondies est d’utiliser le processus de reprise individualisé avec la technologie de polissage à flux continu signée OTEC. Ce procédé de lissage et de rayonnage des arêtes est mécanique, parfaitement fiable et reproductible. Ce traitement ciblé et paramétrable permet au convoyeur à vis de remplir sa fonction sans entraves, sans blocages, sans augmentation de la résistance et sans formation de dépôts.
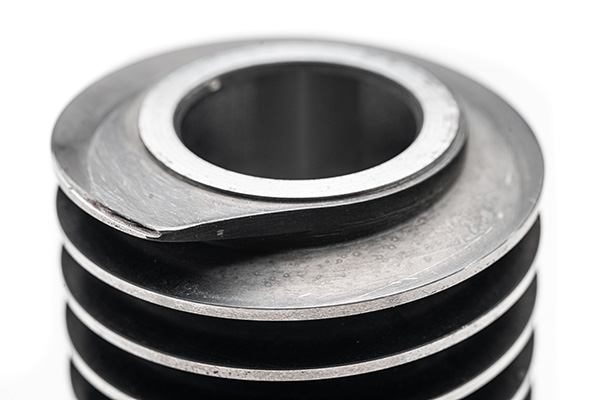
par polissage à flux continu OTEC
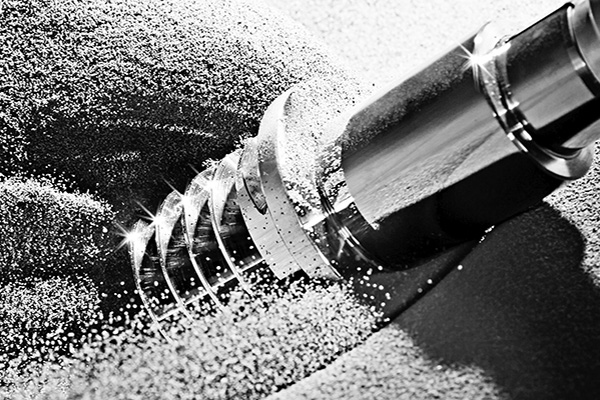
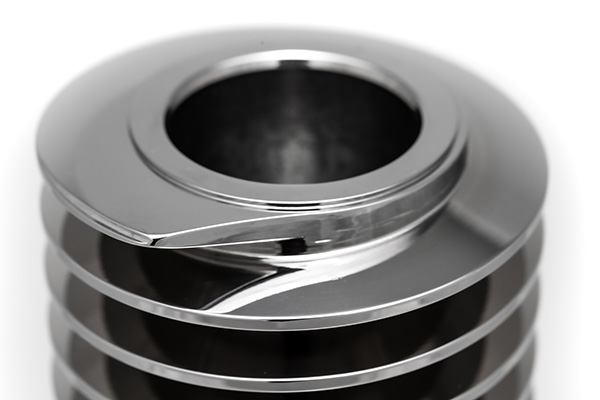
TECHNOLOGIE SCHAAF : LE TRAITEMENT MANUEL APPARTIENT AU PASSÉ
Schaaf Technologie GmbH est un fabricant d’extrudeuses à vis. Jusqu’à présent, le travail de reprise des pièces après tournage et fraisage nécessitait environ 4 heures de travail manuel. Les pièces passaient alors par trois étapes : dans un premier temps, les marques de fraisage le long de l’axe longitudinal étaient supprimées manuellement à l’aide d’une ponceuse à bande. Dans un deuxième temps, une fois le durcissement effectué, la vis était rectifiée sur le diamètre extérieur au moyen d’une rectifieuse cylindrique, ce qui générait, là encore, des arêtes tranchantes. Enfin, il s’agissait de rayonner ces arêtes, puis, avec un papier abrasif assez fin, d’éliminer la couche de calcaire qui se développe à la surface pendant le durcissement, avant de lisser celle-ci. Depuis l’adoption du procédé efficace de polissage à flux continu d’OTEC, la reprise manuelle appartient au passé chez Schaaf Technologie.
Ron Hanke, directeur de production chez Schaaf Technologie :
« Le procédé de polissage à flux continu d’OTEC nous permet de traiter la surface de nos convoyeurs à vis de façon automatique, homogène et parfaitement reproductible. Le tout s’accompagne d’une amélioration générale des propriétés tribologiques avec, à la clé, un allongement de la durée de vie grâce à la réduction des frottements. Le processus ne dure pas plus de 30 minutes et le temps de travail nécessité pour charger la machine est réduit au minimum. Cerise sur le gâteau, la surface obtenue est de meilleure qualité qu’avec un traitement manuel. Le recours au procédé de polissage à flux continu d’OTEC représente pour nous un avantage considérable en termes de qualité et de temps. »
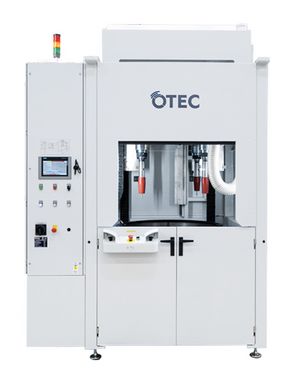
FINI LA LENTEUR
Le procédé de polissage à flux continu (SF) développé par OTEC convient aux géométries particulièrement complexes. Ce procédé consiste à fixer les pièces dans un support avant de les plonger dans une cuve en rotation remplie d’abrasifs ou d’agents de polissage. Comme la pièce est elle-même en rotation, le traitement obtenu est uniforme. Cela permet de produire des surfaces ultrafines avec des profondeurs de rugosité jusqu’à Ra 0,01 µm, y compris sur des géométries complexes. Le tout sans effort physique ni risque de blessure.
Grâce aux forces de traitement appliquées, l’enlèvement de matière est plus ciblé et plus rapide qu’avec n’importe quel autre traitement de surface. La reproductibilité est garantie par la simplicité d’enregistrement et de chargement des programmes de process individuels.
La dernière innovation OTEC SF-HP autorise même l’usinage de grandes pièces d’un diamètre et d’une longueur allant jusqu’à 650 mm chacune et d’un poids maximum de 200 kg.
PROFITEZ DE L’EXPERTISE OTEC
RECTIFICATION ET RAYONNAGE MÉCANIQUES
- Rayonnage ciblé au micron près, adapté à vos besoins/span>
- Arêtes stables et homogénéisées
- Allongement de la durée de vie des pièces et qualité constante
- Pas de contamination du matériau transporté par des fragments d’arête
POLISSAGE ET LISSAGE DE LA SURFACE EN QUALITÉ SPÉCULAIRE
- Moins de produit qui reste sur la pièce
- Amélioration des propriétés tribologiques des pièces
- Réduction des frottements et de l’usure
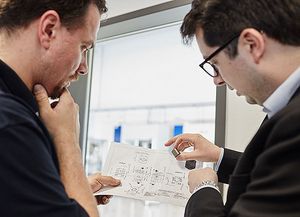
TROUVER LE BON PROCÉDÉ AVEC LES EXPERTS OTEC PRÄZISIONSFINISH
Quelles que soient la géométrie de l’outil et les exigences relatives à la structure de la surface ou au rayonnage des bords, l’équipe d’experts du Centre de finition d’OTEC vous aidera à trouver le bon procédé. Nous trouverons ensemble le procédé le mieux adapté à vos pièces. Prenez directement rendez-vous pour assister au traitement de votre échantillon. Cliquez ici pour en savoir plus sur le traitement individuel des échantillons.