STREAMFINISH - Alternativa ecológica al proceso químicamente acelerado
COMPARACIÓN DE LOS MÉTODOS DE PROCESAMIENTO: PROCESAMIETO DE PIÑONES CON ALTA CAPACIDAD DE CARGA
Existen distintos procedimientos y procesos para el posmecanizado de componentes industriales fabricados en metal. Todos ellos presentan ventajas y desventajas según el tamaño, la geometría, el material y la labor pertinentes. Recurrimos al ejemplo del mecanizado de un piñón para comparar los procesos establecidos en el mercado teniendo en cuenta aspectos como la salud, el medioambiente y la rentabilidad.
UN PIÑÓN, MUCHOS RETOS DE MECANIZADO
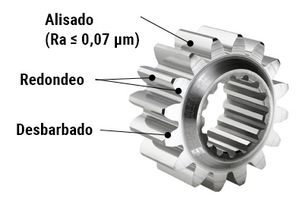
En aeronáutica se emplean piñones con capacidad de carga muy elevada fabricados en acero, rectificados con precisión y altamente endurecidos (>60 HRC). La superficie es resistente y firme, mientras que una estructura superficial en perfecto estado y sumamente isotrópica, es decir, igual en las distintas direcciones, resulta imprescindible para garantizar que puedan cumplir su función de un modo seguro y fiable. Además de contar con un alisado inferior a Ra 0,1 µm, las superficies de la evolvente no pueden presentar ondulación ni ranuras de rectificado. Por otra parte, los bordes de los laterales y del piñón deben presentar un redondeo homogéneo.
NO TODAS LAS VÍAS DE MECANIZADO LLEVAN A LA META
El objetivo está claro: se trata de encontrar el proceso con el que mejor pueda alcanzarse el objetivo.
Una posibilidad es el alisado y redondeo manuales o mecánicos guiados por robots. En este caso, la calidad de mecanizado no es constante durante toda la vida útil de la herramienta, ya que el desgaste progresivo de la muela de rectificado o del cepillo hacen que el acabado superficial sea cada vez menos preciso. Al mecanizar geometrías interiores, ambos procedimientos ofrecen resultados muy irregulares, ya que las herramientas solo se pueden adaptar al componente de forma limitada y la colocación en geometrías estrechas puede resultar difícil o, incluso, imposible. Los componentes con tolerancias muy reducidas se topan con sus límites en el caso de este proceso y, por lo tanto, lo descartan.
El estado actual de la técnica a menudo permite el mecanizado con vibrador de artesa. El uso de determinados líquidos de proceso ácidos reduce el tiempo necesario. Dichos líquidos de proceso pueden contener, entre otros, mezclas de sal de fosfato, ácido fosfórico, ácido oxálico, oxalato de sodio, sulfato, hidrógenocarbonato de sodio, cromato, cromato de sodio, ácido crómico y ácido sulfúrico. La mayoría de estas sustancias son peligrosas y hay que ser especialmente precavidos al manipularlas. En concreto, el cromato (de sodio) y el ácido crómico están clasificadas como sustancias extremadamente preocupantes, carcinogénicas, mutagénicas y tóxicas para la reproducción (cromato de sodio) en virtud del Reglamento REACH (Registration, Evaluation, Authorisation of Chemicals). Tanto el ácido sulfúrico como el ácido oxálico y el ácido fosfórico, además del cromato de socio y el ácido crómico ya mencionados, se consideran sustancias cáusticas y, en algunos casos, tóxicas. Por lo tanto, la mayoría de estas sustancias se ha clasificado como sigue de conformidad con el sistema de etiquetado de sustancias peligrosas SGA:
- Toxicidad aguda
- Peligro para el medioambiente acuático
- Distintos riesgos para la salud
- Corrosión de metales, corrosión cutánea, lesiones oculares graves
El proceso satisface los requisitos de mecanizado, pero, por lo general, el líquido de proceso solo se puede usar una vez y debe sustituirse una vez concluido este. Conlleva costes muy elevados de adquisición, neutralización y eliminación que limitan la rentabilidad. Además, el uso de sustancias peligrosas oculta riesgos como los antes indicados para la salud de las personas y para el medioambiente.
En el mercado también se ofrece el llamado proceso de electropulido para pulir piezas de metal en un único paso. Funciona con electrolito, lo que permite alcanzar y mecanizar incluso geometrías interiores. Una desventaja considerable de este procedimiento consiste en que los procesos de rectificado de conformación no pueden eliminar la ondulación que se genera durante el proceso de electropulido, ya que la capacidad de desbaste es, sencillamente, insuficiente. La duración promedio del proceso abarca de 30 minutos a varias horas. Además, según el proceso, solo se mecanizan a fondo las zonas expuestas. Tras el tiempo de uso prescrito deberá desecharse el electrolito como residuo especial y volver a adquirirse de nuevo, lo que supone un gasto considerable.
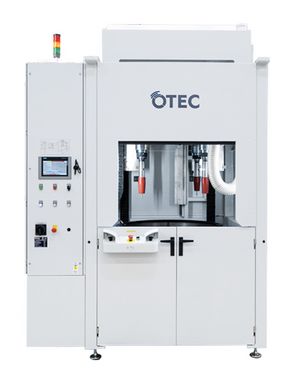
STREAMFINISH: ALTERNATIVA ECOLÓGICA
Vaya por delante que Streamfinish alcanza resultados similares a los del rectificado químicamente acelerado, pero que el proceso es puramente mecánico y no utiliza ácidos ni granulado electrolítico, lo que aumenta la rentabilidad del posmecanizado.
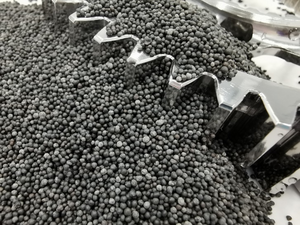
¿POR QUÉ FUNCIONA STREAMFINISH?
El proceso Streamfinish que ha desarrollado OTEC engancha los componentes en un soporte y los sumerge en un recipiente lleno con medio de rectificado o pulido que gira sobre sí mismo. El giro adicional de la pieza y el movimiento relativo que este genera entre el componente y el medio permiten lograr un mecanizado homogéneo sin intervenciones manuales. De este modo, se alcanzan superficies de alta precisión con durezas de hasta Ra 0,01 µm incluso en geometrías complejas.
Las inmensas fuerzas de mecanizado permiten eliminar el material de forma más rápida y precisa que con cualquier otra clase de mecanizado superficial. Un medio fino alcanza las geometrías interiores y las mecaniza sin dificultad alguna.
MARCHA SOBRE RUEDAS: PIÑONES RESISTENTES AL DESGASTE GRACIAS A STREAMFINISH
Durante la interacción de los piñones, una película lubricante reduce la fricción y el desgaste. En el procedimiento Streamfinish se crean bolsitas microscópicas en la superficie de las que sale lubricante y que, por lo tanto, constituyen una ventaja de proceso, puesto que, si la superficie es demasiado lisa y plana, puede producirse una rotura de la película lubricante entre dientes que enganchen entre ellos, lo que supondrá un accidente del engranaje y, con ello, un fallo total.
Los piñones mejoran de forma global cuando se mecanizan con el proceso Streamfinish. Con esto nos referimos al aplanamiento de la superficie y a la eliminación de puntas duras o estrías de mecanizado. Así se obtienen tanto una superficie isotrópica como la dureza acordada con el cliente. Los piñones que se mecanizan con el proceso Streamfinish quedan preparados para su uso posterior («rodadura») gracias a la gran energía de fricción que reciben. Además de reducirse la fricción y el desgaste, se crea una capa de cizallamiento en la superficie. En dicha capa se generan cambios en la estructura y tensiones de compresión residual que acondicionan el piñón en gran medida para su uso.
STREAMFINISH EVITA LOS DESECHOS
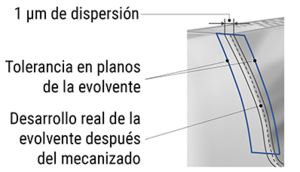
El proceso Streamfinish alcanza una dispersión de proceso sumamente reducida de tan solo 1 µm: en comparación con el proceso acelerado químicamente, la dispersión en este caso es entre cinco y diez veces inferior.
Para la producción, esto implica que está disponible gran parte del intervalo de tolerancias del proceso de rectificado de conformación anterior. Así, es posible evitar totalmente la eliminación debida a la dispersión elevada del proceso de acabada. En el caso de los piñones rectificados con alta precisión, esto supone un ahorro de hasta cinco cifras por instancia.
EJEMPLO DE APLICACIÓN DE UN PIÑÓN SOMETIDO A CARGAS ELEVADAS
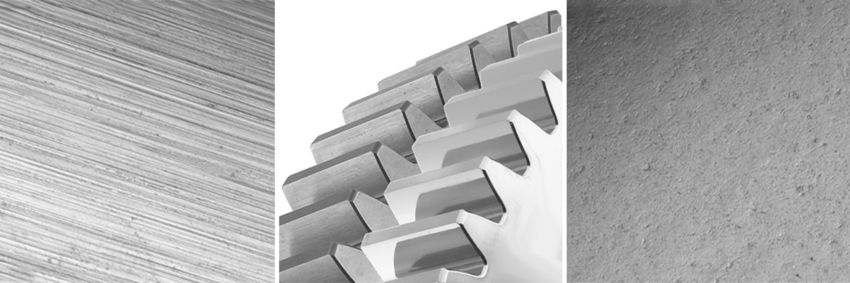
Antes:
Ra 0.19 µm
Rz 1,358 µm
Rpk 0,418 µm
Después:
Ra 0,042 µm
Rz 0,551 µm
Rpk 0,139 µm
Estado initial
- Acero, endurecido, 60+ HRC, piñón rectificado con alta precisión
- Dureza inicial: Ra de 0,19-0,21 µm
- Duración del proceso: 20-35 min
Resultado de mecanizado
- Superficie sumamente isotrópica
- Dureza final: Ra 0,042-0,084 µm
- Eliminación de surcos y estrías
- Redondeo homogéneo de los bordes
- Variación muy limitada de los procesos
- Creación de bolsas microscópicas de lubricante en la superficie
DISFRUTE DE LAS VENTAJAS DE STREAMFINISH DE OTEC
- Desbarbado rápido y eficiente, redondeo de bordes y alisado en un único paso
- Variación muy limitada de los procesos (1 µm) en comparación con la de otros procesos (~5-10 µm)
- Seguridad máxima de los procesos gracias al uso de mezclas de servicio
- Superficie sumamente isotrópica
- Sin picos de dureza (Rpk <0,1 μm): menor desgaste, no se requiere rodadura, duración más prolongada del aceite
- Menor riesgo de micropicadura
- Proceso rentable, ya que es circular
- No se requiere una eliminación costosa de los medios del proceso
- No hay que manipular sustancias químicas peligrosas
- Tiempos de mecanizado muy breves: cuatro veces más rápido que el proceso químicamente acelerado
Streamfinish resulta apto, entre otros, para componentes con geometrías complejas, con un peso de hasta 200 kg y un diámetro de hasta 650 mm, como discos de turbina, palas de turbina, blisks, servoválvulas o piñones para la aeronáutica.
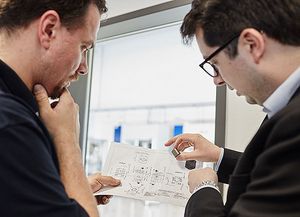
SELECCIÓN DEL PROCESO CON LOS EXPERTOS EN ACABADOS DE PRECISIÓN DE OTEC
Con independencia de las geometrías. los requisitos de la estructura superficial y la labor de mecanizado, el equipo de expertos del OTEC Finishing Center le ayudarán a seleccionar el proceso. Juntos encontraremos el proceso adecuado para sus componentes. Concierte una cita directamente para presenciar la creación de una superficie perfecta en sus componentes.
Más información sobre la definición de procesos individuales >>