STREAM FINISHING - the green alternative to chemically accelerated processes
Processes in comparison: Processing of highly loades gear wheels for aerospace
There are numerous methods and processes available for post pro-cessing industrially manufactured metal components, with various advantages and drawbacks de-pending on the size, geometry, ma-terial and finishing requirements. We look at four well-established processes on the market for fin-ishing gear wheels and assess them in terms of health and safety, environmental impact and cost-effectiveness.
ONE GEAR WHEEL – MANY PROCESSING CHALLENGES
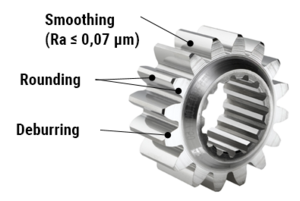
Many highly loaded steel gear wheels are produced for use in the aerospace industry that must be ground to an extremely high degree of precision and hardened to levels greater than 60 HRC. The surface of a gear wheel is solid and tough. If it is to function safely and reliably later on, the surface structure must be flaw-less and extremely isotropic, meaning it must be highly uniform in all directions. As well as requiring a roughness of below Ra 0,1 µm, the involute surface must not be wavy or show any grinding grooves. In addition, the edges on the sides and on the tooth head must be evenly rounded.
NOT ALL PROCESSING METHODS HIT THE MARK
Now we know the criteria, we need to identify which process comes out top where it really matters. One option is manual or mechanical robotic smoothing and rounding. Here the processing quality through-out the tool’s life cycle does not remain constant, as progressive wear on the grinding wheel or brush re-sults in an ever more imprecise surface finish over time. Both methods produce very uneven results when processing inner geometries because the tools can accommodate different components only to a very lim-ited extent, and are difficult, if not impossible, to position in tight places. Components with very narrow tol-erances lay bare the limitations of these methods, which cannot process them effectively. Current technology often favours trough vibrators for processing. Using certain acidic process liquids can help to reduce process times. The types of liquids used include mixtures containing phosphate salts, phos-phoric acid, oxalic acid, sodium oxalate, sulphate, sodium bicarbonate, chromate, sodium chromate, chro-mic acid and sulphuric acid. Most of these substances are hazardous and employees require special pro-tective equipment when handling them. (Sodium) chromate and chromic acid have been classed as sub-stances of very high concern by the REACH regulation (Registration, Evaluation, Authorisation and Restriction of Chemicals) as they are carcinogenic, mutagenic, and in the case of sodium chromate, toxic to reproduction. Along with sulphuric acid, oxalic acid and phosphoric acid, they are also skin sensitis-ing and, in some cases, toxic. For this reason, the Globally Harmonized System of Classification and Labelling of Chemicals (GHS) has listed the following properties for most of these substances:
- Acute toxicity
- Hazardous to aquatic environment
- Various other health hazards
- Skin irritant that is corrosive to metal and may cause serious eye damage
Whilst this process might tick all the boxes in terms of finishing requirements, the process liquid can gen-erally only be used once and must be replaced once processing is finished. This results in increased pur-chasing, neutralisation and disposal costs, meaning the process is far from cost-effective. As we have al-ready seen, the use of these hazardous substances also brings with it health and safety and environmental risks.
Dry electropolishing processes are another option available on the market for polishing metal workpieces in a single operation. They use electrolyte granulate to reach and process even inner geometries. However, not all granulate is suited to the workpiece shape, and electrolyte can get jammed in the workpiece. One of the biggest drawbacks is that this electropolishing method cannot remove the waviness caused by the forming process of grinding as its abrasion level is simply too low. The average process time ranges from 30 minutes to several hours. What is more, by nature of the process, only the exposed areas can be properly finished. The electrolyte granulate must also be disposed of as hazardous waste once it has reached the end of its given service life, and buying new granulate to replace it is an additional financial burden.
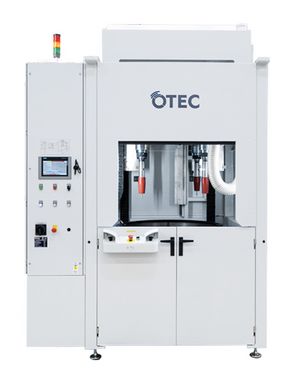
Stream Finishing - a green alternative
One thing is clear: Stream Finishing results are on a par with those of chemically accelerated mass finishing. But the key difference is that Stream Finishing is a purely mechanical process that does not use acids or electrolyte granulate, making post-processing much more cost-effective.
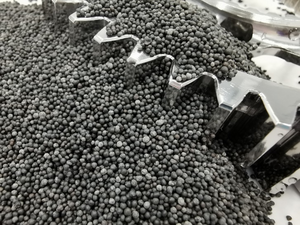
HOW DOES STREAM FINISHING ACHIEVE SUCH GOOD RESULTS?
In Stream Finishing, which was developed in-house by OTEC, the components are clamped in a holder and immersed in a rotating container filled with an abrasive or polishing medium. The workpiece itself also ro-tates, and the relative motion between the component and the media produces an even finish without the need for manual work. The process turns out highly precise surfaces with a roughness as low as Ra 0.01 µm on complex geometries.
The enormous machining forces used in Stream Finishing can remove material faster and more accurately than any other type of surface processing. The fine media used can get through to the inner geometries and process them without difficulty.
GETTING INTO GEAR: WEAR-RESISTANT GEAR WHEELS COURTESY OF STREAM FINISHING
Lubricating film can help to reduce wear and friction between gear wheels. During Stream Finishing, micro-scopic lubrication valleys are produced on the workpiece surface. These are very beneficial as they can re-tain lubricant. If the surface is too smooth and flat, the lubricating film between the interlocking teeth can break, resulting in the seizure and complete failure of the gearbox.
Stream Finishing improves the overall surface quality of the gear wheels by levelling the surface and remov-ing roughness peaks and machining grooves to produce an isotropic surface, and an agreed roughness based on the customer’s requirements. It employs high friction energy to prepare the gear wheels for use when they are later run in. In addition to reducing friction and wear, the process also produces a shear layer by changing the surface structure and creating compressive residual stress, which is highly effective in conditioning the gear wheel for use.
STREAM FINISHING REDUCES REJECT RATE
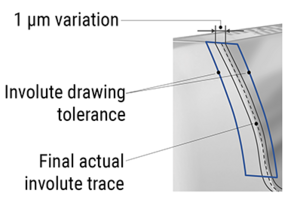
Our Stream Finishing process boasts an extremely low process variation of just 1 µm – which is five to ten times lower than chemically accelerated processes.
This is good news for the production process as it means that there is greater leeway to use the tolerance range in the upstream forming process of grinding. Having to reject workpieces due to high variation during the finishing process is now a thing of the past. When gear wheels must be ground to an extremely high degree of precision, reducing the reject rate can save tens of thousands per reject.
APPLICATION EXAMPLE FOR A HIGHLY LOADED GEAR WHEEL
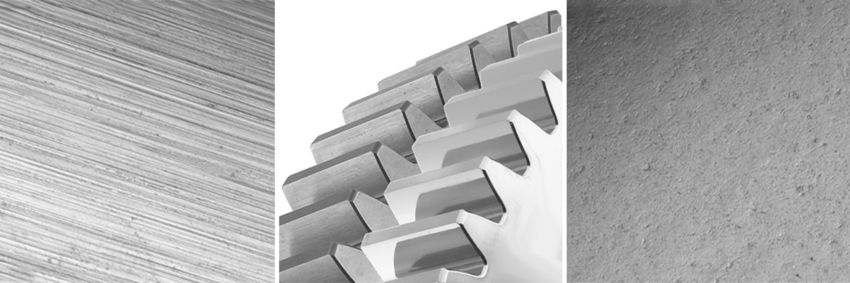
Before processing (left):
Ra 0.19 µm
Rz 1,358 µm
Rpk 0,418 µm
After processing (right):
Ra 0,042 µm
Rz 0,551 µm
Rpk 0,139 µm
Initial condition
- Gear wheel made of hardened steel, 60+ HRC, ground to an extremely high degree of precision
- Initial roughness: Ra of 0.19 – 0.21 µm
- Process time: 20 - 35 mins
Processing result
- Extremely isotropic surface
- Final roughness: Ra 0,042–0,084 µm
- Striations and grooves removed
- Uniform edge rounding
- Very low process variation
- Microscopic lubrication valleys produced on the Surface
THE BENEFITS OF OTEC’S STREAM FINISHING
- Rapid and efficient deburring, edge rounding and smoothing in one single step
- Very low process variation (1 µm) compared with other methods (~5–10 µm)
- Exceptionally high process reliability obtained by mixing new and reused grinding bodies
- Extremely isotropic surface
- No roughness peaks (Rpk < 0,1 μm): less wear, no run-in necessary, longer oil service life
- Low risk of micropitting
- Cost-effective process suitable for recirculation
- No expensive disposal of abrasives
- No handling of dangerous chemicals
- Very short processing times – four times quicker than chemically accelerated processes
Stream Finishing is suitable for a variety of components, including those with complex geometries, a weight of up to 200 kg and a diameter of up to 650 mm, such as turbine discs, turbine blades, blisks, servo valves and gear wheels for the aerospace Industry.
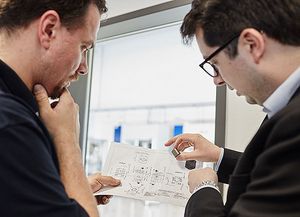
DEFINE YOUR PROCESS WITH THE HELP OF OTEC PRÄZISIONSFINISH EXPERTS
Our specialist team at the OTEC Finishing Center is ready to assist in defining your process – whatever the geometry, surface structure or finishing requirements. Work with us to identify exactly the right process for your component. Arrange an appointment today to experience perfect surface processing tailored to your component. More >>