Screw caps for bottles: High efficiency and process reliability with polished moulds
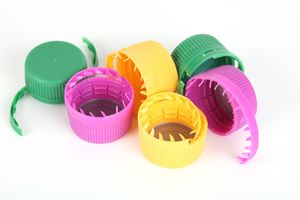
To produce them cost-effectively you need to keep rejects to a minimum. And that’s where high-quality precision moulds make all the difference, because the better the quality, accuracy and service life of the mould, the more efficient your mass production.
The special moulds used for screw caps are usually turned from steel and then milled or injection moulded. In one mechanical post-processing stage (or two depending on the application), the mould is smoothed and polished so that the plastic caps produced on it will separate without sticking or residues, and without affecting the cap geometry. So the smoother the surface, the longer the mould provides top performance.
STREAM FINISHING + PULSE FINISHING = superb surface quality (Ra < 0.1 μm) in seconds!
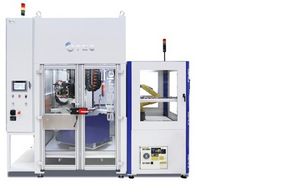
Pulse finishing, OTEC’s stream finishing innovation, has remained the fastest mass finishing pro-cess on the market ever since it was launched in 2013. With average process times of 60 seconds, it’s (literally!) rapidly putting conventional techniques in the shade.
The process obtains uniform results even on complex workpieces like moulds for screw caps, be-cause it’s highly effective at using very small grinding bodies.
All omformations about SF-Series >>
(Technologie, models, brochures as download and more