With accurray down the last micron, surface problems on stablished knee implants are a thing of the past
The knee joint is a hinge joint that also allows a certain degree of rotation. It’s also the largest hinge joint in the human body. Knee prostheses come in various forms, but for patients with unstable ligaments or bone loss, doc-tors use the stabilised type, also known as axially supported. The two components (the femoral im-plant and the metal platform) are joined by a stabilising hinge. The functional feature of these prostheses is a “box” with inner geometry (see Image). And therein lies the mechanical processing challenge, because conventional techniques quite literally can't hit the target.
It's all about the angle
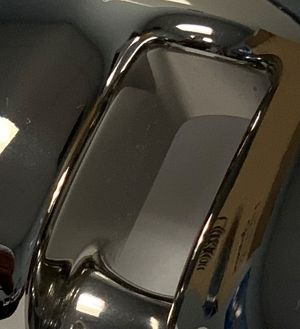
OTEC Präzisionsfinish has the solution: stream finishing – the technology behind a whole new gen-eration of mass finishing machines. In this procedure, the workpieces are clamped in a holder and lowered into a rotating container filled with an abrasive or polishing medium. The workpiece rotates and is processed as the medium circulates around it. SF is capable of performing multiple pro-cessing steps very quickly in a single operation, which means a workpiece can be rapidly deburred, rounded, smoothed and polished in sequence and with no additional workload. When it comes to in-ner geometries like those on stabilised knee implants, this has two key advantages: first, a contour-controlled motion sequence and second, an adjustable workpiece angle. These features make it possible to target the media flow at specific sections of a workpiece for particularly intensive pro-cessing. And that translates to effective results in minimal time. Material abrasion can be controlled and it's also possible to set precise roughness parameters based on the process: with initial work-piece values of Ra 0.8–1.2 µm you can achieve outstandingly smooth target values of up to Ra 0.01 µm.
The benefits at a glance: processing stabilised knee implants with OTEC stream fin-ishing technology on the SF-3/3:
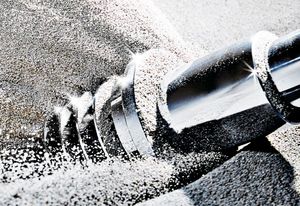
- Uniform surfacesConsistent workpiece Quality
- Process reliability
- No manual finishing
- Up to three knee joints in one pass
- Process/process time in two steps:
1. Wet grinding approx. 40–60 min; 2. Dry polishing approx. 16–20 min - No programming required
It runs like clockwork: SF Series automation with Robot Loading System (RLS)
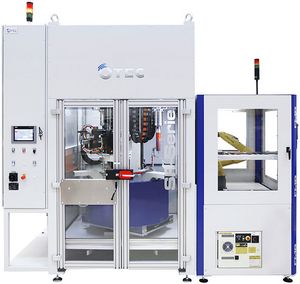
When processing large volumes of workpieces, short loading and set-up times make your operations far more efficient. That’s where our automatic robot loading system comes in (the SF RLS, see left). SF Automation Series machines can be fitted with optional pulse finishing and work well, for example, in cyclic production lines. Depending on your requirements, the machines can either be set up for automatic loading or fitted with it as an integrated option. The machine design is modular and therefore easy to adjust to cycle time. The SF Automation can thus be easily integrated as a key element of any production line.
Give your surfaces an OTEC precision finish
At OTEC, we aim to deliver not just the right machine and holder for each workpiece and surface finishing requirement, but also the ideal abrasive and a customised process. We adapt, or indeed develop, a specific solution based on your needs. Put us to the test: send us some samples and our inhouse Finishing Center will specify your individual process. To ensure that it’s reproducible and efficient, with perfect surfaces every time, we'll establish and professionally document all the relevant process technology parameters.