Aerospace Specialist IFT opts for an OTEC finish
The exacting safety, precision and quality standards of the aerospace industry are as stringent as it gets. Every single manufacturing step has to be closely monitored and documented. Not every production facility can meet these multi-level requirements. OTEC customer IFT GmbH & Co. KG, based some 30 miles south of Frankfurt in Ober-Ramstadt, specialises in high-precision parts for the motorsport, medical technology and aerospace industries.
“Technical innovations and reliable process performance in the surfacing tech-niques and systems we use are essential because we’re constantly optimising our portfolio. We’re uncompromising in our choice of machinery and processes. They have to be absolutely right for the order and help us deliver the quality, ef-ficiency, fast turnarounds and absolute deadline reliability that we promise our customers. We also review existing processing steps again and again to see how we can improve them,” explains IFT Junior General Manager Robin Breitwieser.
OTEC disc finishing machine up to 20 times more effective than trough vibration? Challenge accepted!
“OTEC assured us that surface processing with its disc finishing machines was up to 20 times more effective than conventional trough vibration. That sparked our curiosity. Our trough vibration processing time for aerospace hydraulic con-trol pistons was four hours, which was simply too long. With these particular workpieces it was all about deburring and smoothing – we wanted to deliver better surfaces without compromising the sharpness of the edges. So the spec-ifications we gave the experts at the OTEC Finishing Center were exacting down to the last micron, because precise surface roughness and edge rounding meets the quality our aerospace customers demand, and which of course we always aspire to meet,” sums up Breitwieser.
OTEC accepted the challenge. At our Finishing Center in Straubenhardt on the edge of the Black Forest, we processed some samples free of charge using the SF Series disc finishing machine with zero-gap system for both applications. Fifteen minutes later we delivered the goods to specification – complexity and all!
Each OTEC machine also has a process tailored to the workpieces and pro-cessing requirements it’s designed for. With deburring, for example, choosing the right grinding bodies is vital. It's essential that burrs are ground off rather than kinked or bent. That requires extensive experience and specialist knowledge. Our process development expertise is second to none, which makes us the ideal partner to help specify the right abrasive and system for the job.
Fast and flawless: OTEC mass finishing machines
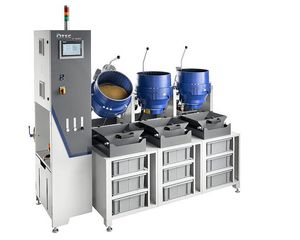
CF Series disc finishing machines are designed for rapid, flawless surface pro-cessing on a wide variety of workpieces such as fine blanked, turned, milled and punched parts as well as jewellery.
Workpieces are processed in an open container that has a disc-shaped floor with a rotary bearing. They are added to the fixed container along with a suita-ble grinding or polishing granulate. When the disc turns, the contents are set in motion in a toroidal flow. Centrifuging the granulate and workpieces makes this process highly intensive – up to 20 times more effective than conventional vi-brators, for example.
All Information about CF Series >>
All OTEC Videos on OTEC YOUTUBE Channel >>
About OTEC Präzisionsfinish
OTEC GmbH Präzisionsfinish provides precision technology for achieving perfect surfaces. OTEC machines are used for smoothing, precision edge-rounding, polish-ing and deburring a wide variety of workpieces, with the aim of improving surface quality. With a network of international business partners, OTEC has a global pres-ence. OTEC’s comprehensive, market-leading technical expertise in developing the perfect interplay of machine and abrasive benefits a wide range of industries includ-ing tooling, medical devices, jewellery, and automotive and aerospace.