Valve Spools
Smoothing for high contact ratio
In hydraulics, proportional valves are predominantly used when controllable volume flows are required. The spool in the valve regulates the flow. It acts as a shut-off body, by closing or releasing the inlet and outlet openings. The edges of the valve spool play a major role in sealing the openings. In the manufacturing process, the surface quality of the spool is vital. It is not only important to deburr and smooth the valve spool, but also perform defined rounding of the edges. By smoothing the roughness peaks high contact ratios are achieved, leading to less friction and less wear. The result is a more reliable sealing surface. The smooth surface also ensures less leakage when overflowing and lower leak oil values. Deburring, rounding and smoothing of the valve spool reduces friction on the valve.
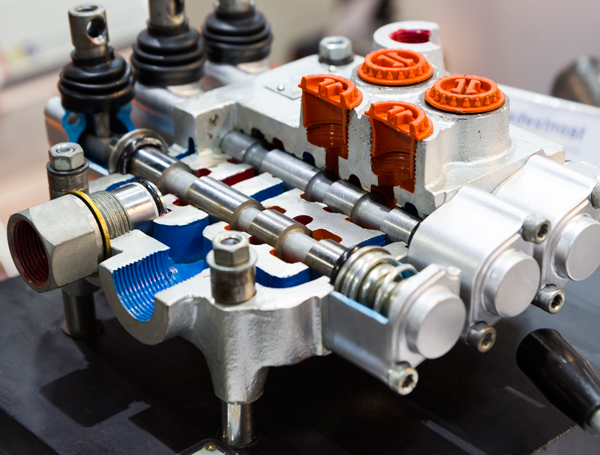
Previous methods of manufacturing valve spool, used processes such as sandblasting or brushing for surface treatment. However, the achieved results from the techniques are often not reproducible, meaning further process steps are necessary to achieve a satisfactory surface quality. In addition, conventional methods often cause difficulties in the subsequent cleaning process.
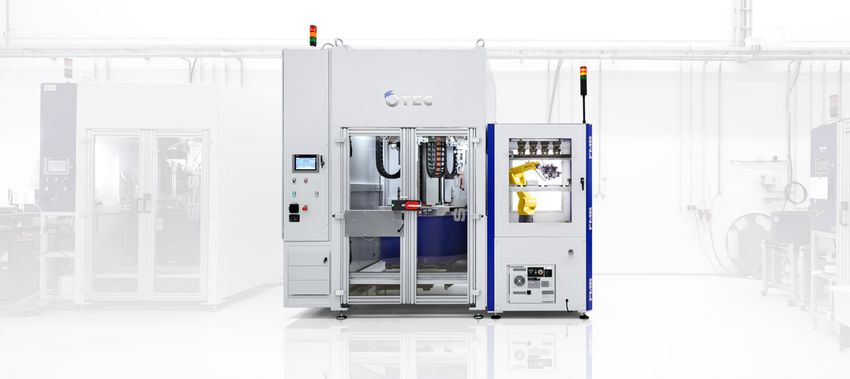
In stream finishing systems from OTEC, high machining forces are applied, which enable valve spools to be smoothed, deburred and rounded quickly, reliably and in a single, easily repeatable, operation. The spool is clamped into a holder, rotated and immersed in a rotating container with grinding media. Processing is carried out by abrasive media flowing around the workpiece as well as by the rotating workpiece. The stream finishing process achieves uniform material removal. The controllable movement sequence allows the edges of the valve spool to be rounded in a targeted manner. Depending on the geometry and the initial state of the workpiece, the process equipment and process parameters will be individually adjusted. With the OTEC stream finishing machines, it is possible to carry out several processing steps in one go without additional effort. Short processing times, high reliability and easy automation makes stream finishing an extremely economical surface treatment method. The machine can be equipped with automatic loading by robot and three independent lifting units. This makes it possible that while two workpieces are being processed, a workpiece change can take place at the third station in parallel. This significantly reduces change-over times to a minimum while ensuring and high output and productivity. Depending on the desired result, geometry and initial condition of the workpiece, the processing times of valve spools take as little as three to six minutes.