Streamfinish in the automobile manufacturing
Fully integrated into line production
OTEC’s stream finishing and pulse finishing units have been specially tailored to the requirement profile of assembly line production in the automobile industry or high-tech tool industry, in order to meet the high standards of process reliability, speed and processing quality demanded by large-scale series production.
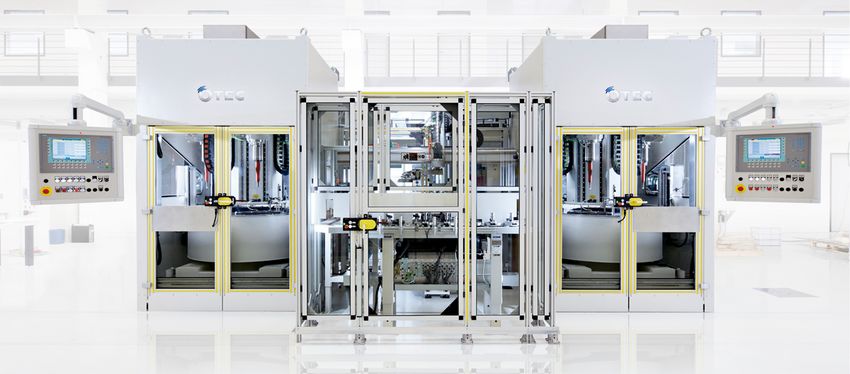
STREAM FINISHING MACHINE TYPE SF4/140
We developed the Type SF 4/140 stream finishing machine with pulse drive especially for full integration into the production lines of large-scale automotive series production plants. This system type enables our customers to deburr, round and smooth camshafts simultaneously and in a very short time. With the aid of a central handling cell made by our partner Felsomat, two Type SF4/140 stream finishing units are loaded and unloaded automatically. The loading and unloading is carried out by way of automatic lift doors at the stream finishing machines. The transfer from the system to the main portal is effected via a separate conveyor belt integrated into the handling cell. This plant layout enables eight workpieces to be processed at the same time, giving a cycle time of 17 seconds. The complete unit linked in this way measures approx. 6,5 x 3,5 x 3,1 m. Control panels fitted to the side of the support arm make the system easy to operate. Of course, individual adjustments can be made to suit the customer’s wishes and requirements. The workpieces are clamped by means of collet expanding mandrels. The rotating workpiece is finished by being immersed in a stream of polishing medium. The stream is generated by a rotating process drum. After finishing, the workpieces are blasted clean and returned to the customer’s process by means of a separate conveyer system. In this way, 3,500 – 4,000 workpieces can be finished daily.
Result
Smoothing of the surface from Rz 2.5 μm to less than 1 μm and Rpk value to less than 0.1 μm.
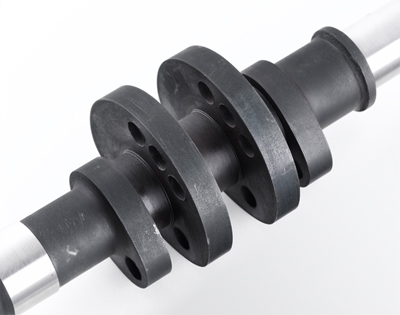
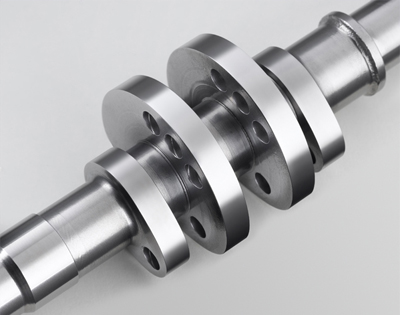
PULSE FINISHING MACHINE TYPE SF3
The company developed the pulse finishing process specially for assembly line series production in the automotive supplier industry. In this process, the workpiece is clamped to a spindle and lowered into a drum containing an especially fine-grain abrasive medium. The drum rotates around its own axis at speeds of up to 60 rpm. The spindle holding the workpiece oscillates at about 2,000 rpm, i.e. it accelerates to 2,000 rpm within one second, then decelerates and accelerates again to 2,000 rpm. and so on. In addition, the spindle can be swivelled through up to 25 degrees so that the stream of abrasive medium to the workpiece can be adapted to the specific geometry of the workpiece. “The processing time for reducing the roughness value from, for example, 0.2 μm to 0.1 μm, is less than a minute”, says OTEC CEO Helmut Gegenheimer in explanation of the strengths of this machine concept. Depending on the number of spindles, the cycle time is from 20 to 25 seconds. In the finishing center, OTEC determines the exact processing time, the best process media and the right machine parameters for each workpiece.
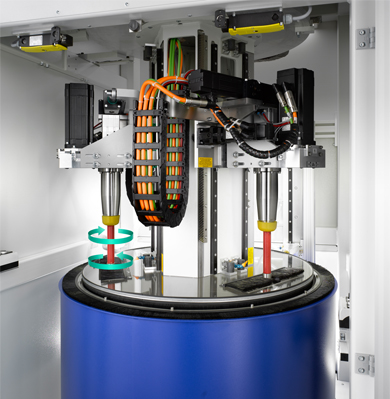