SMOOTHING
OTEC can generate extremely flat surfaces through mass finishing, surfaces which are perfect for bearings because they have a very high contact surface ratio which in turn drastically reduces abrasion and noise generation. In this process, the peaks of the surfaces are reduced to Rpk <0.1 µ and the striae which act as oil pockets are retained. Our process and the resultant surface reduces wear and consequently increases tool life.
In the automotive industry in particular, our pulse finishing process is used because it has proven to be an extremely cost-effective method. Low unit costs, fast tooling-up times and short cycle times are the key features of the patented pulse finishing process. Forming tools are mainly finished in our stream finishing and drag finishing units in order to increase their service life and performance. Our patented driven holder gives very fast and uniform finishing, attaining Ra values of up to 0.01 µ. Typical applications include the following:
- Motor racing (e.g. for smoothing and polishing gear wheels, valves, rocker arms, pistons, expansion screws and camshafts)
- Automotive (e.g. for smoothing and polishing camshafts, gear wheels, drive units and worm shafts)
- Metalworking industry (e.g. for smoothing high-speed spindles)
- Forming tools (for smoothing and polishing the pressing and forming surfaces)
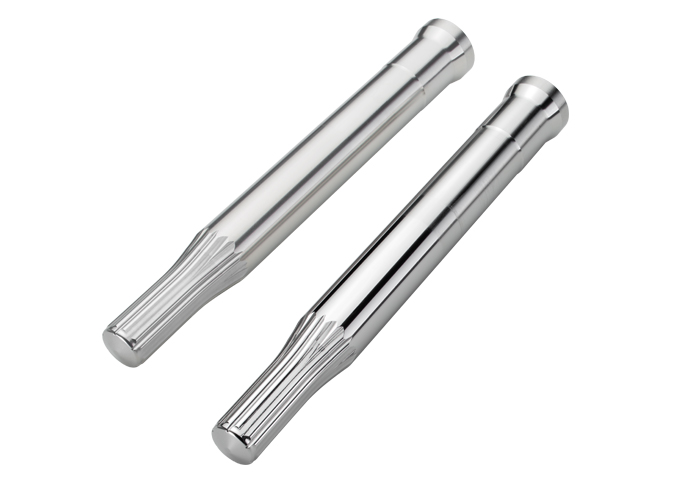